reliability design, additive manufacturing, lightweight construction
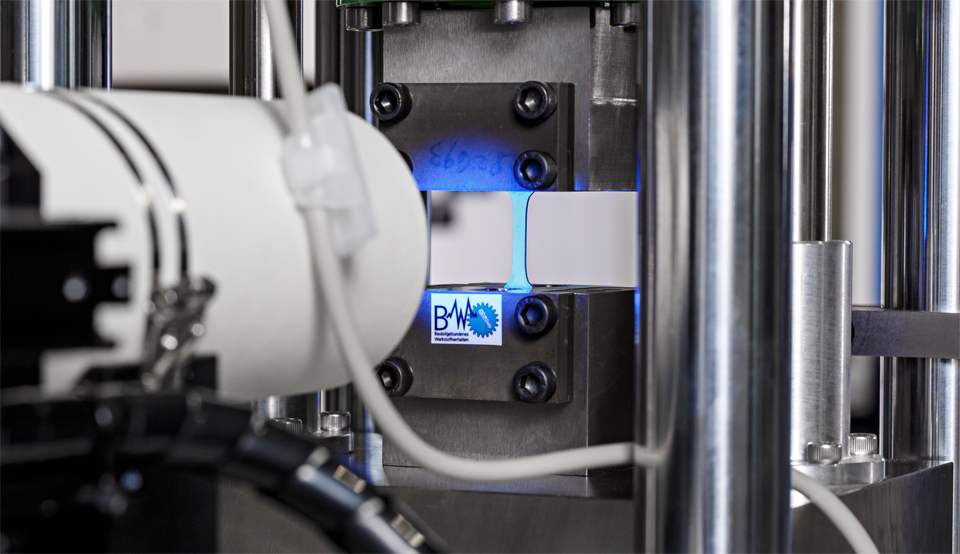
In the AM FATIGUE LABS, realistic simulations are developed that show reliable design characteristics for the design of additively manufactured components. They also ensure design validation by taking the influence of all relevant process parameters into account. Specially-developed load simulators increase the precision and reproducibility of the measurements. This insight into the cyclic material and component behavior would be almost impossible using classical testing methods.
To also be able to exploit the advantages of additive manufacturing for safety-relevant components, in terms of lightweight construction, many challenges have to be met in the alternating field of component geometry, manufacturing, operational stresses and environmental influences.
The realization that component fatigue is driven by local phenomena is becoming increasingly important, especially for additively manufactured components. The new levels of freedom in component development require a new design concept to be able to leverage the potential of this manufacturing technology for cyclically stressed, safety-relevant components as well. On the one hand, the manufacturing process induces geometric defects in the form of pores, inclusions or rough surfaces; on the other hand, the very limited local heating leads to the formation of significant property gradients. Here, factors including the direction of construction and the design of the required support structures also play a significant role in the formation of the material microstructure, thereby affecting the local properties, including the defect distribution.
In the AM FATIGUE LABS, the Fraunhofer LBF team uses a range of optical strain sensors whose measurement signals have the required real-time capability. In this way, strain control is made possible, for example, in component areas that are relevant for failure. At the same time, the researchers derive information about the local damage mechanism from the synchronous-load measurement of local strain fields. This information can be used for component optimization. What is more, it can also be used to increase material utilization by taking defect-oriented material behavior into account in early design phases.
Dr. Rainer Wagener