Design of plastic tanks
Fraunhofer LBF improves 2D tensile test and modelling in design of plastic tanks
Design of plastic components is primarily based on the methods developed for ductile metals. Applied to plastics these methods provide errors in components subjected to multi-axial tensile loads. The adjusted methods require the test results under 2D and 3D tensile loads, which cannot be gained from the uniaxial tensile tests. Scientists at the Fraunhofer Institute for Structural Durability and System Reliability LBF have improved known test specifications for the biaxial tensile test under the effect of temperature. The implemented optical measurement during the loading allows the precise acquisition of the mechanical response of the plastic sheets. The data from the new test method improves the material modelling thus providing the basis for an enhancement of the design quality of plastic components.
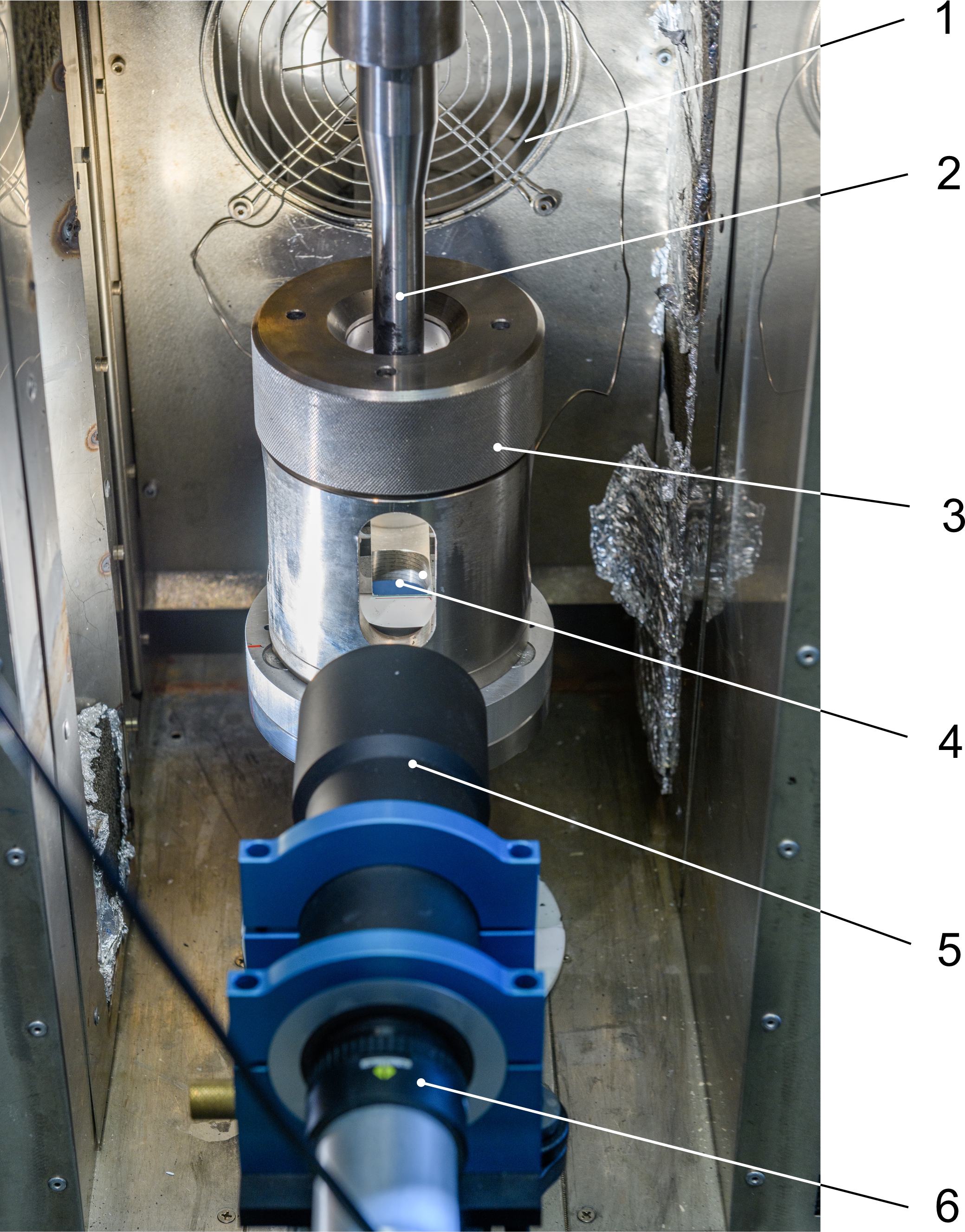
Established methods in design are commonly based on the uniaxial tensile test. Applied to plastic components, such methods are critical. Especially for tanks under internal pressure, vessels, valves, or in components of undersee applications, such designs cause “unexpected” failures in service. The aim is therefore to provide industry decisive information on the mechanical behaviour under multi-axial tensile loads. The methods should be clear and affordable. The new Fraunhofer LBF method supplies both data for reliable modelling of components under loading and appropriate design tools. In this way, parts for automobiles, components in aircraft construction or products for sports, medicine, and household can be designed more reliably and more cost-effectively.
Refined method for 2D tensile test
The test setup was designed to be applied to standard plastic plates of about 2 mm thickness, that are commonly used for the extraction of specimens for plastic testing. The plastic plate is firmly clamped in the test fixture between circular rings and centrally loaded with an indenter, causing the deflection of the specimen. A balanced (uniform) biaxial tensile stress occurs in the centre of the specimen. The contact area is lubricated to reduce friction. Stress singularities in the clamping area are reduced by a special design of the edges of the circular rings.
The deformation of the sample is captured by a CCD-camera with a telecentric lens to eliminate virtual strain that occurs when the viewing plane shifts along the optical axis. The strain evaluation of the geometry change in the plate is performed in a subsequent post-processing step using the grey scale correlation software. Additionally, a second CCD-camera is used to capture the beginning of the plasticization at the edge of the clamping.
The test results can be evaluated up to an approximate bending of the plate of 6 mm. Various forms of the deflection lines can be obtained by varying the diameter of the fixture and the diameter of the hemisphere. Optimal diameters are proposed by our scientists, according to the material properties, the sample thickness, and testing needs. The tests are performed according to customer specifications or our standards with temperatures up to 120 °C.
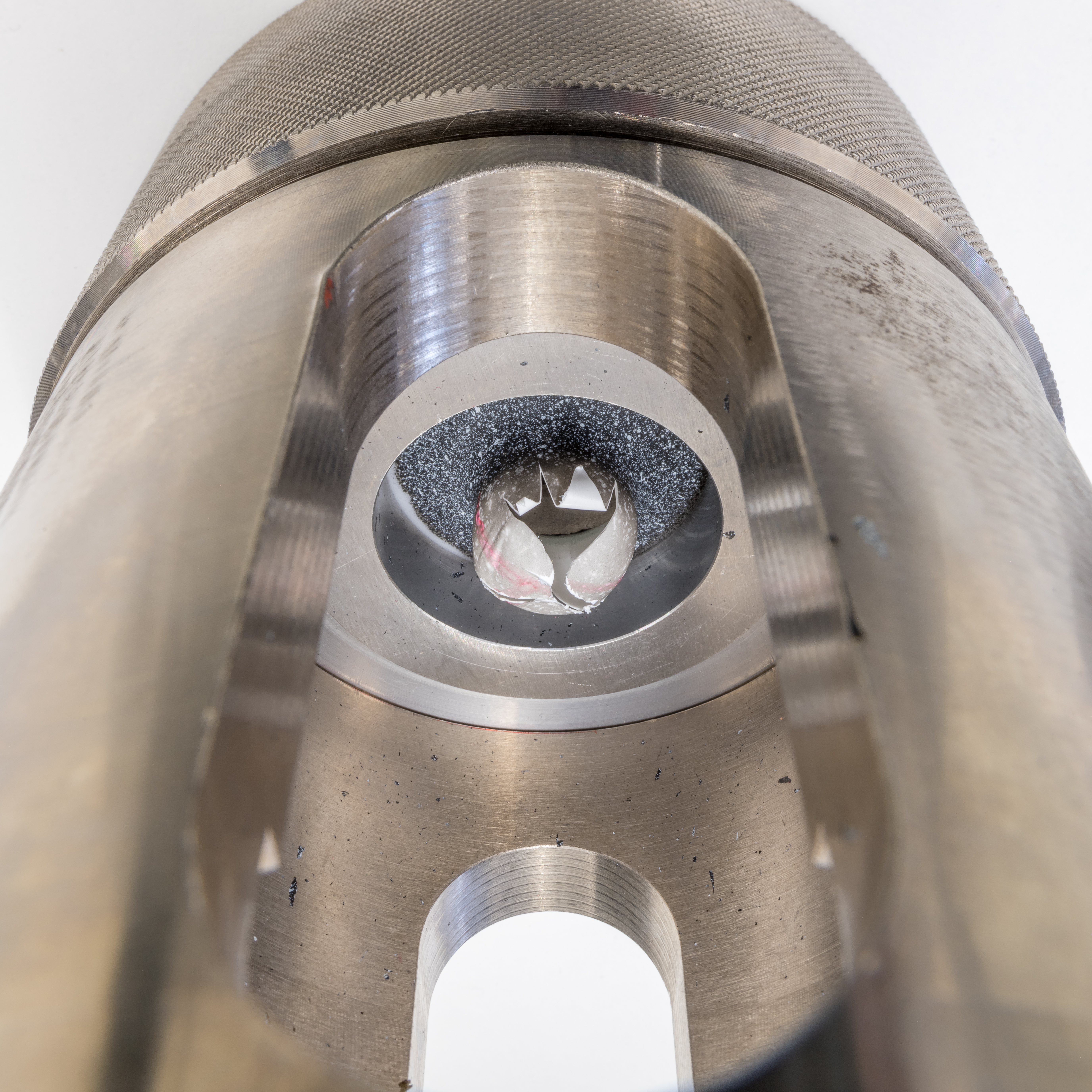
Evaluation of deformation by digital image correlation
The thickness of the specimen is measured before the test. The specimen is speckled with a statistically distributed black & white pattern and then tested directly to ensure optimum adhesion between the plate and the pattern until failure. This allows the evaluation of strains on the specimen surface by digital image correlation as function of the total force. In addition, the setup allows to capture the local effects and examine the unloading behaviour of the polymers. Also, the test specification enables to obtain the creep properties under 2D tensile loading.
Total force versus deflection as a function of the radius are evaluated by reverse engineering methods. Good agreement between the experimental and the simulation results at different temperatures can be found. These data are used e. g., for design and investigation of the failure cases in plastic tanks under inner pressure and elevated temperatures. Material models and generalised strength criteria with minimal number of the parameters adapted to the plastics are implemented and fitted based on the gained test data. Our scientists analyse the individual challenges in the modelling of the critical plastic components and provide expertise at all levels of the design process.
Last modified: