Automotive Testing
Optimized component testing and validation
Numerical simulations have massively accelerated product development over the past few decades. A variety of scenarios can be tested in a short time and the number of necessary prototypes has been steadily reduced. Nevertheless, physical tests are widespread and will not lose significance over the next few decades. Numerical models must be validated and approval testing must be carried out. Depending on the modeling complexity, the physical test can also be more cost-efficient. In the recently completed project “Digitization in Testing Technology”, scientists from the Fraunhofer Institute for Structural Durability and System Reliability LBF addressed the question of how physical testing can benefit from methods from the numerical world. What is the optimal combination of real and virtual world? Tunable test rig components and a mechanical hardware-in-the-loop approach have been developed. They make it possible for mechanical parameters such as stiffness rubber mount properties and structural dynamic effects to be set quickly and without modifications to the test rig. This facilitates rapid parameter variations to the test rig and further provides a new, energy-efficient interface between numerical real-time simulation and testing bench. The Fraunhofer LBF will present the results at the Automotive Testing Expo in Stuttgart from May 21-23, 2019 in hall 8, booth 8052.
New test rig components for faster development and validation

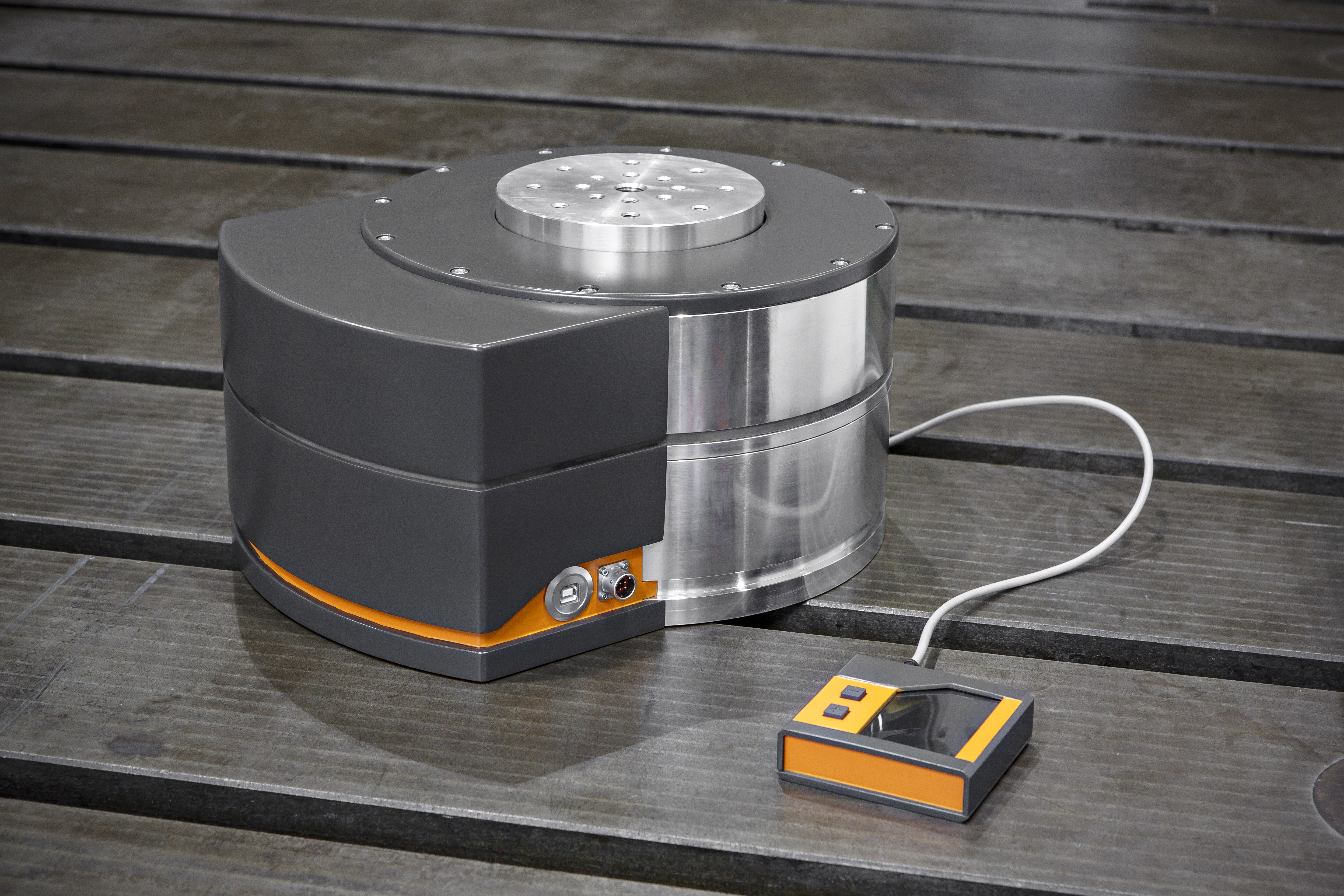
The research team from Darmstadt developed tunable components and a mechanical hardware-in-the-loop interface. Tunable components allow continuous adjustment of mechanical characteristics. For example, mounts with tunable stiffness enable testing of a test specimen under different boundary conditions or the implementation of tunable vibration absorbers.
If tunable rubber mounts are used as a development tool, with stiffness and damping adjustable independently of each other, it is possible to forgo the first bearing prototypes. This makes it possible to provide the mount manufacturer with optimized specifications at an early stage of development. Mechanical hardware-in-the-loop interfaces can be used to simulate more complex boundary conditions in experiments, especially in the field of NVH development. The interface behaves equivalent to a underlying numerical model in a wide frequency range. For example, an adaptive shock absorber can be tested for different combinations of top mount and chassis without carring out any modifications to the testing bench.
»The transfer of numerical simulation methods into the physical world of testing makes it possible for development processes to be drastically accelerated and costs to be reduced. Furthermore, our technologies and test rig components offer new possibilities for validation of numerical simulation models. Models can be validated for different operating points with less effort«, says Jan Hansmann, research associate and project manager at the Fraunhofer LBF. Next, the research team from Darmstadt wants to work on the series-production implementation, which requires close cooperation with industrial partners.
Automotive Testing Expo, 21.-23.5.2019
Last modified: