replacement test, connection stiffness, operational strength test
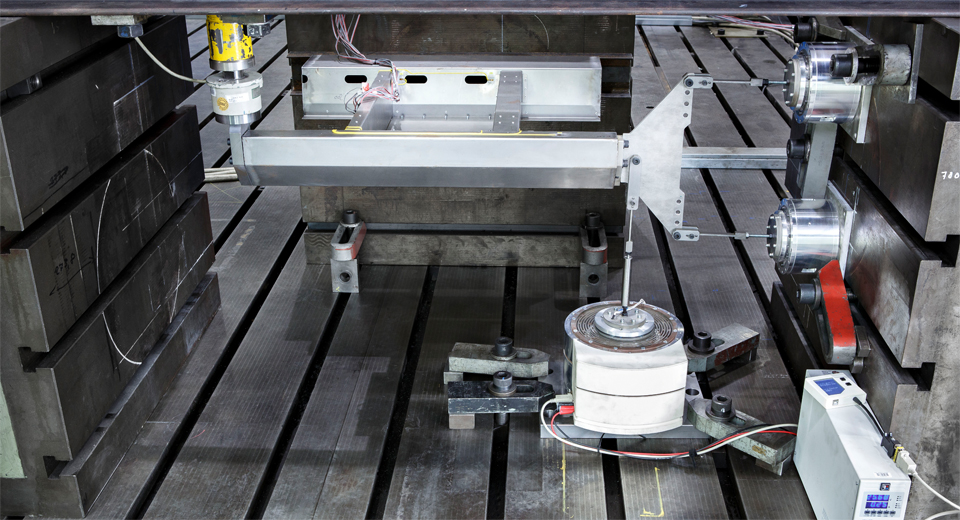
Using the example of a vehicle floor of an electric vehicle, which accommodates the battery cells, the integration and demonstration of a workflow for developing and realizing a realistic test could be shown. This floor structure must endure large mechanical loads, such as the twisting of the bodywork that results from driving over a pothole. In the demonstration testing bench, a realistic component load was generated for this purpose. However, only one of the six segments of the floor structure is available for testing, as opposed to the entire body.
A numerical model of the overall structure is used to determine the strain that would occur in the test specimen during operation. In addition to the external load, this is also influenced by the stiffness of the surrounding structure, which is simulated in the test setup by bearing points with adjustable stiffness. This is followed by a digital model of the test setup with adjustable boundary conditions. Here, there is also a cost-benefit analysis.
The use of adjustable mounts and programmable interfaces allows for the parameters to be varied quickly without modification work. It is only necessary to set the desired stiffness on the mount or load the numerical target model of the vehicle to be simulated. The stiffnesses of adjustable mount and mHIL interface are continuously adjustable between 0.4 kN / mm and “rigid” (> 60 kN/mm).
Testing substructures with adjustable stiffness boundary conditions makes it possible to validate components and assemblies earlier in the product development process. It is also possible to test larger quantities at the substructure level, which leads to better statistical validation of service life. The adjustability of the equivalent stiffness elements also enables easy testing of the assembly for different variants of the surrounding structure, such as different body versions. Overall, the adjustable connecting elements therefore enable successful completion of product validation at a faster pace.