Prediction based on chemical structure and mechanical properties
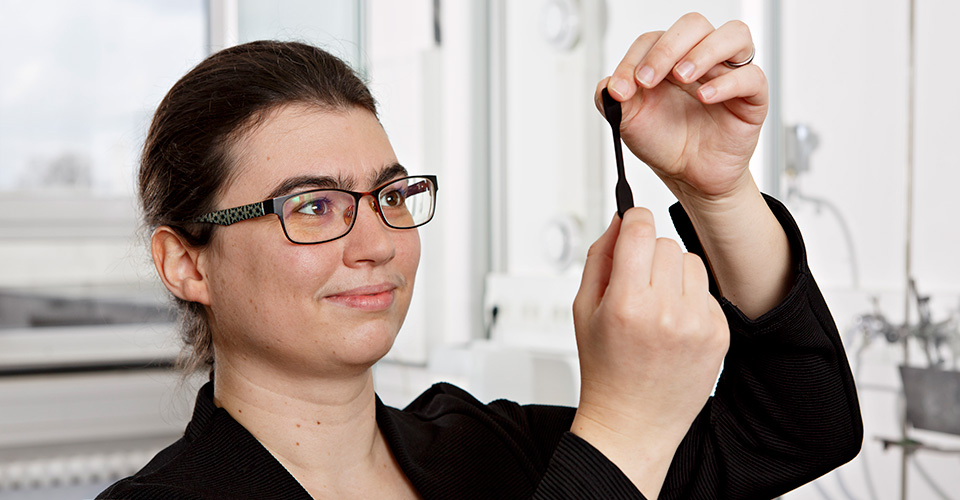
ProElasto
The material properties of an elastomer are essentially determined by the cross-linked polymer structure. The mesh size of the network (degree of cross-linking) and the type of network nodes (sulfur bridges of different lengths) are two important structural variables of sulfur cross-linked elastomers. By varying the amount of cross-linking chemicals (sulfur and accelerator), it is possible to specifically produce elastomer materials with varying degrees of cross-linking and a different average sulfur bridge length for network nodes.
The cross-linked elastomers are characterized using a variety of physical measurement methods. The focus of physical characterization is on (quasi-)static tests, such as hardness or the classic tensile test, but also on dynamic experiments, such as dynamic mechanical analysis (DMA). In addition, the compression set is measured and stress relaxation experiments with stepwise tensile tests are performed. Using mathematical models, the measured mechanical properties can be correlated with the degree of cross-linking and average sulfur bridge length as structural variables (Fig. 2 as an example for hardness).
To determine the service life of the material, cyclic fatigue tests are performed at two load levels and used to calculate a Wöhler curve. The number of cycles to failure at a fixed load level can be correlated with the degree of cross-linking and the average sulfur bridge length, as can the mechanical properties. A longer service life can be achieved either with a lower degree of cross-linking or with a longer average sulfur bridge length.
To make a prediction, the number of cycles to failure at a fixed load level is plotted as a function of the corresponding property. The hardness, ultimate strain and static modulus show a linear dependence in relation to the length of service life (log(N)). In this case, the determination of the service life becomes more accurate for higher load levels. The linear relationship with the compression set is particularly good, i.e., with low scatter, regardless of the load level (Fig. 3).
It is therefore possible to estimate the service life based on the mechanical properties, provided that sufficient data is available for a correlation. The next step is to determine the extent to which the results can be transferred from the elastomeric compound investigated to other elastomeric compositions. The aim here is to carry out as few tests as possible. In addition, it might also be possible to include other structure-determining influences, such as the processing conditions, in a model for predicting the service life in cyclic fatigue tests.
With our in-depth knowledge of how compound components, production conditions, chemical material structure and various material properties influence each other, the research work carried out by Fraunhofer LBF along the production chain aids the development of customized durable elastomer components.