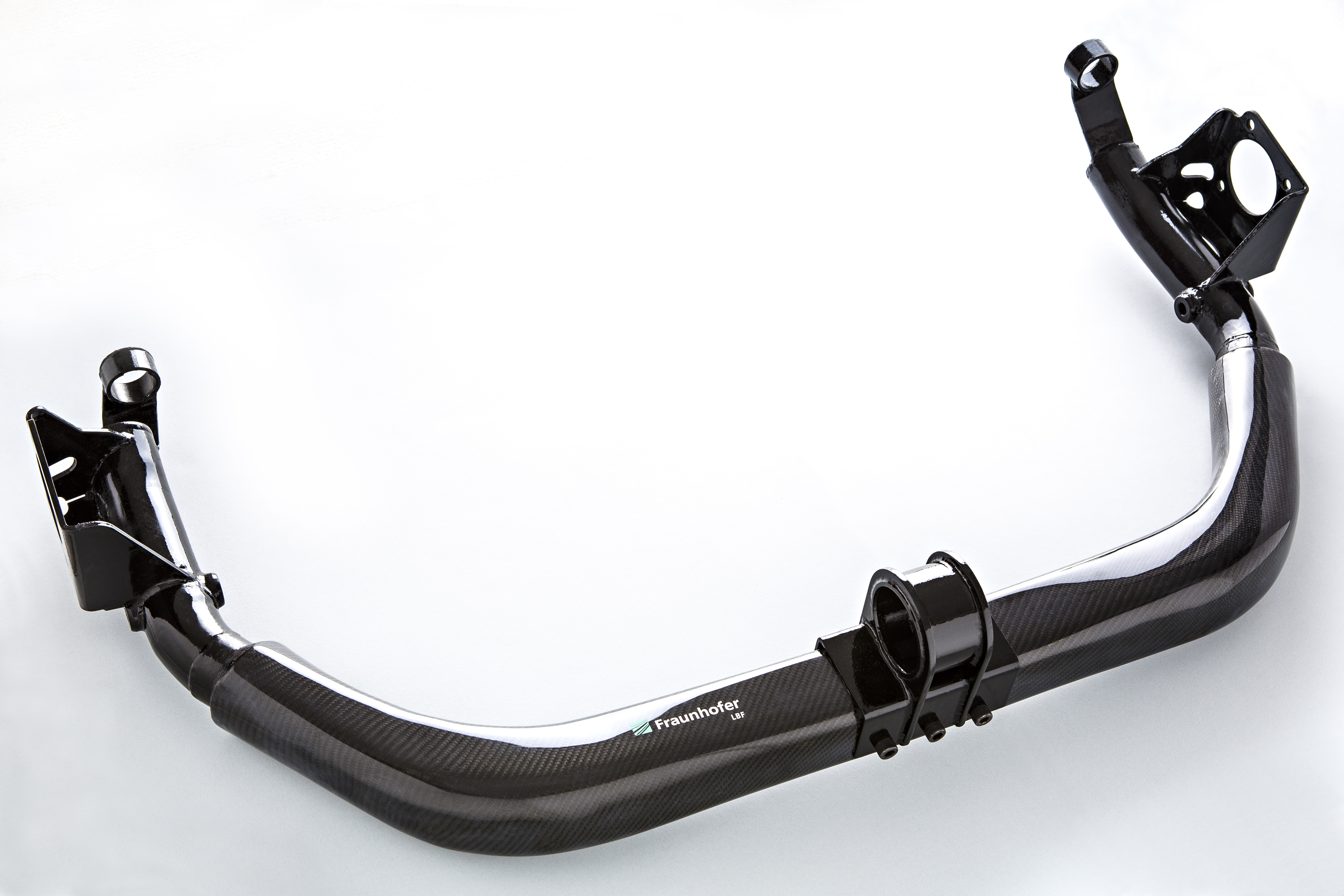
Entwurf, Nummerische Simulation, Prototypenherstellung
Im Rahmen des EU-Projekts epsilon beschäftigte sich das Fraunhofer LBF mit der Entwicklung und Fertigung einer neuartigen Fahrwerkskomponente, einer Hinterachse. Dabei sollten die Aspekte des Leichtbaus und der Fahrtüchtigkeit einen besonderen Schwerpunkt bilden. Um das Ziel des Projekts zu erreichen, bestand die Notwendigkeit, eine umfangreiche Studie über das Leichtbaupotenzial der Vorder- und Hinterachsen durchzuführen. Die Aufgabenstellung wurde mithilfe der Verbundbauweise und dem Einsatz von faserverstärkten Kunststoffen gelöst.
Leichtbau spielt nicht zuletzt durch die aufstrebende Elektromobilität eine wichtige Rolle. Die Erhöhung des Gesamtfahrzeuggewichts durch die nötigen Akkumulatoren in Elektrofahrzeugen stellt die Automobilhersteller vor eine enorme Herausforderung. Auch bei konventionellen Fahrzeugen mit Verbrennungsmotor spielt die Leichtbauweise aufgrund der immer höheren Anzahl von Zusatzfunktionen und der damit verbundenen Erhöhung der Gesamtmasse eine große Rolle. Aufgrund dessen befassen sich immer mehr Entwickler und Hersteller mit der Aufgabe der Gewichtsoptimierung und setzen dabei innovative Lösungen ein. Karosserie- und Fahrwerksbauteile, die früher aus Metallwerkstoffen hergestellt wurden, werden zunehmend häufiger durch Kunststoffteile und Faserverbundteile substituiert.
Die entwickelte hybride Leichtbauhinterachse beinhaltet eine Reihe von innovativen Lösungen:
Im Laufe des Projekts erfolgte die Berechnung der Hinterachse mittels der FE-Methode in mehreren Schritten. Parameterstudien und Konstruktionsvarianten führten schließlich zu einem optimierten Entwurf. Dieser besteht aus zwei metallischen Seitenteilen und einem Mittelteil aus Faser-Kunststoff-Verbund. Durch diese Hybridbauweise wird die Gestaltung der Anbindungsstellen an die Fahrzeugstruktur vereinfacht und Temperatureinflüsse bzw. Beanspruchungen können besser berücksichtigt werden. Durch den FKV-Mittelteil reduziert sich das Gesamtgewicht der Hinterachse um ca. 37 Prozent.
Da die Leichtbauhinterachse auch noch im Fahrversuch geprüft werden soll, lag bei der Auslegung ein besonderes Augenmerk auf der Sicherheit und der Einsatztauglichkeit des Bauteils. Aufgrund fehlender Vergleichswerte von ähnlichen Hinterachsen mussten die Sicherheitsfaktoren für die Auslegung entsprechend hoch angesetzt werden. Nach den Fahrtests besteht aber die Möglichkeit, über eine nachfolgende Optimierung der Geometrie das Leichtbaupotenzial der Leichtbauhinterachse noch besser auszuschöpfen.