Local vibration resistance assessment through image correlation and AI support
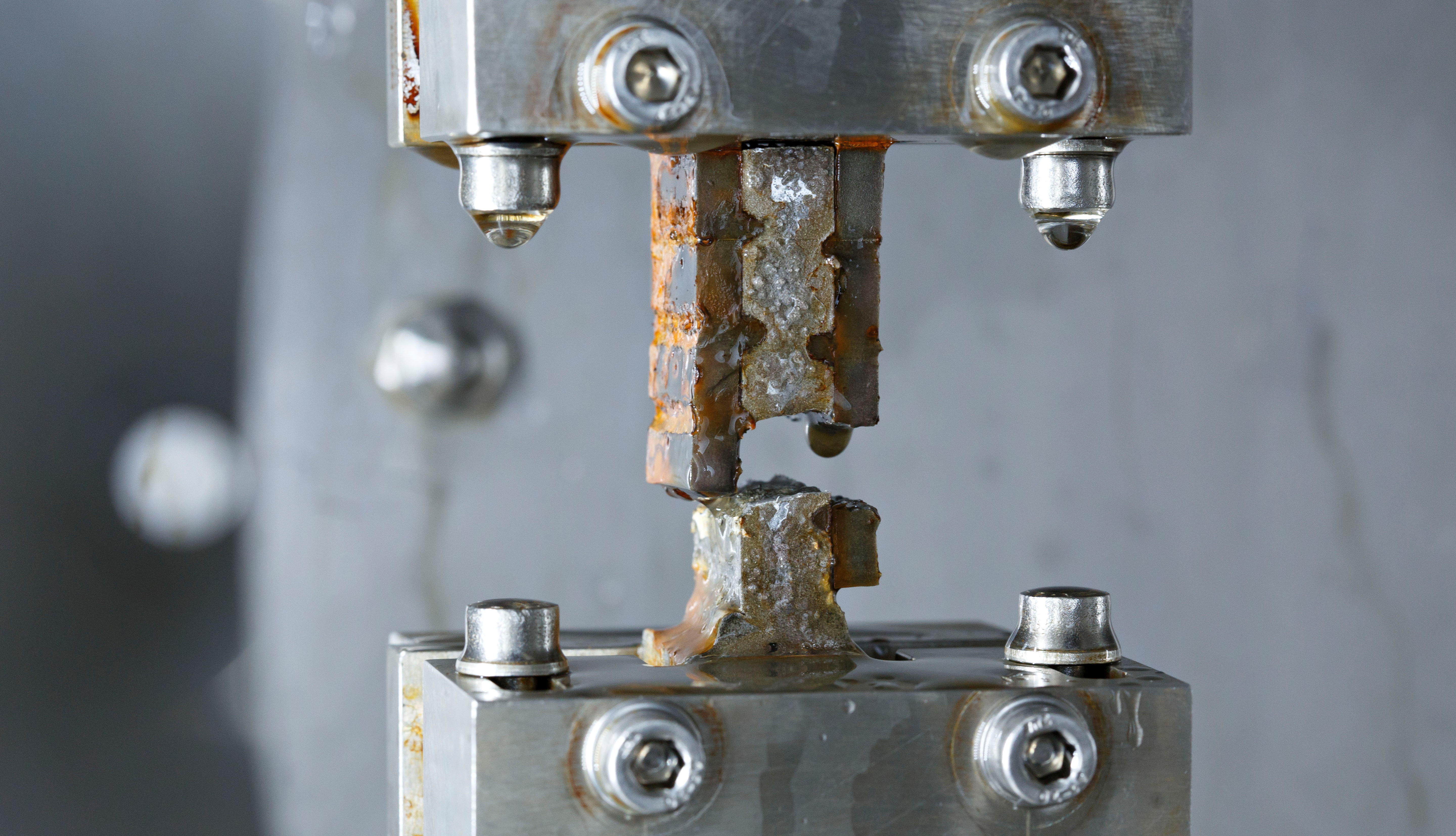
In the “FOLAMI” research project, Fraunhofer LBF focused on evaluating mixed steel and aluminum joints produced by form-fitting laser beam welding for durable semi-finished products in shipbuilding. Accompanying the welding process development, numerical and experimental investigations were carried out to verify the structural durability, initially at the sample level and then for specifically optimized adapters as connecting elements between steel and aluminum structural elements.
Im Forschungsprojekt »FOLAMI« hat sich das Fraunhofer LBF der Bewertung der durch formschlüssiges Laserstrahlschweißen erzeugten Mischverbindung aus Stahl und Aluminium für betriebsfeste Halbzeuge im Schiffbau gewidmet. Begleitend zur Schweißprozessentwicklung dienten numerische und experimentelle Untersuchungen dazu, die Betriebsfestigkeit zunächst auf Probenebene und anschließend für spezifisch optimierte Adapter als Verbindungselemente zwischen Stahl- und Aluminium-Konstruktionselementen abzusichern.
In shipbuilding, especially in yacht building, multi-material joints are already widely used when lightweight aluminum is combined with conventionally processed steel materials. This steel-aluminum composite joint has been realized to date in the form of explosion-welded adapters, also known as explosive cladding. Alternatives to this manufacturing process are motivated by increased costs or design and functional limitations. Laser beam welding can lead to an alternative manufacturing process as a novel welding method.
During the development of the welding process, Fraunhofer LBF initially supported the optimization of the weld seam geometries and subsequently the welding process parameters by means of numerical stress simulations. The focus of the research work was on developing a methodology for evaluating steel-aluminum laser welded joints and implementing it in a welded adapter. For this purpose, a local evaluation method, the so-called peak stress method, was transferred to the application case of steel-aluminum mixed joints with the aid of digital image correlation for strain matching.
The evaluation procedure developed by the research scientists at LBF involves correlating the weld seam parameters, such as the bond width or weld penetration depth of the laser weld seam of EN AW-6082 T6 aluminum in S355 steel, with the fatigue strength derived using the peak stress method and verified experimentally. To expand the database beyond the test results, parameter variations of the weld seam geometries and finite element stress simulations were carried out to derive peak stresses, which are divided into a training and test data set for predicting the service life using a neural network.
The research results not only provide an evaluation approach for this specific steel-aluminum composite, but also offer the potential for transferability to other joined metallic multi-material compounds. Against this background in particular, this evaluation method can be transferred beyond applications of welded joints in shipbuilding to applications in other industries.
The joint research project Form-locked laser beam welding of mixed steel and aluminum joints for durable semi-finished products in shipbuilding (FOLAMI), subproject Evaluation of mixed steel and aluminum joints produced by form-locking laser beam welding for durable semi-finished products in shipbuilding (grant number 03SX547C), conducted by Forschungszentrum Jülich GmbH (PtJ), was funded by the German Federal Ministry for Economic Affairs and Energy as part of the research program Maritime Technologies of the Next Generation based on a resolution of the German federal parliament (Bundestag).
Duration: June 1, 2021 – December 31, 2024
Project partners: