Optimized Specimen for In-Plane Shear Test
For quality control and damage assessment of injection-moulded components, simple and cost-effective tests are desired. Preparation of the standard test specimens is sometimes costly. In this case, the specimens taken from the flat areas of the component can be preferred. Scientists at the Fraunhofer Institute for Structural Durability and System Reliability LBF have improved known in-plane geometry for the shear test. Together with the modified loading schema, the new procedure is reliable and can be used for a wide range of materials. The new test specification is especially developed for SME's to reduce the costs of the component development and also by quality control. With this method, the data for material appropriate modelling can be obtained. The manufacture of special test specimens is obsolete.
In context of realistic loading scenarios, the in-plane-shear test offers one of the easiest possibilities of the materials survey. But the known test specifications are restrictive. Fraunhofer LBF has modified the known test specification so that the measuring region of the specimen is enlarged and the stress concentrations by the force introduction are significantly reduced. In this way, parts for automobiles, components in aircraft construction or products from sports, medicine, and household can be can be designed more reliably and more cost-effectively.
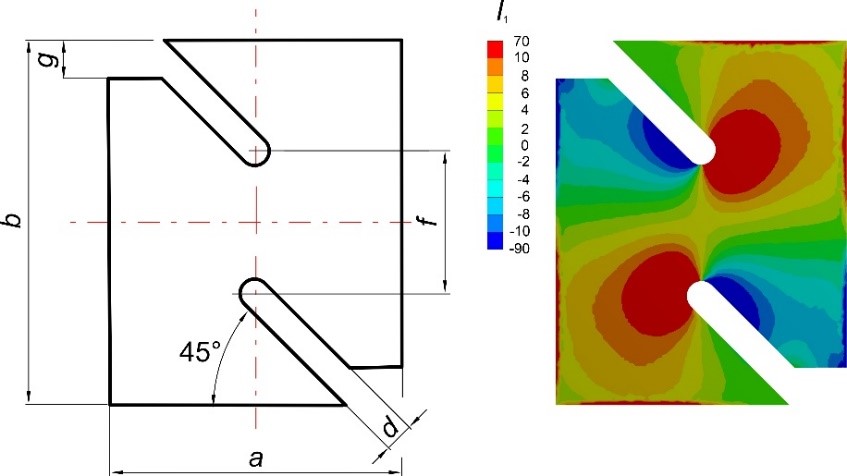
In-Plane Shear Specimen
Slotted shear specimens have been established for material characterization in research and commercial applications. This test specimen is loaded on tension in the vertical direction. Field under shear stress will accrue between the notch tips. The deformation gradients are recorded during the test and evaluated subsequently with digital image correlation.
Reliable implementation of the test requires correct positioning of the specimen in the fixture and skilled personnel to perform the evaluations. Due to the stress concentrations in the tip of the notch, this test is suitable for relatively ductile materials. Some limitations arise when being used for short fiber reinforced thermoplastics and laminates.
For the simple stress analysis of the specimen, we use the sum of the normal stresses or the first invariant of the stress tensor I1. This sum is equal zero in the case of the shear loading. For reliable test results the shear field must be increased and the stress concentrations significantly reduced.
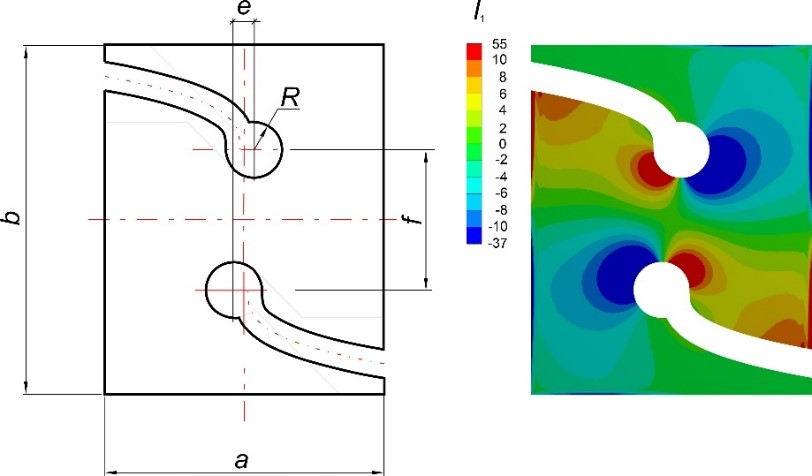
Optimized Geometry of Specimen
At Fraunhofer LBF researchers managed to develop a novel shear specimen that overcomes the major drawbacks of the known specimens. Special geometric and loading design allows homogenized shearing field and reduced tensile stress concentrations in the tip of the notches.
The comparison of the areas with I1=0 shows an increase of the shear region in the measured field. The tip of the notch in the modified geometry is under compression. It is visible that the stress peaks are reduced.
This shear test can be performed in the conventional tensile testing machine. Stability loss of specimen is excluded constructively. The tests can be carried out under the influence of temperature and time. The relaxation experiments provide the data for the material cards of the commercial FEM codes. An extended shear field increases the accuracy of the measurement. This test is feasible for a different class of materials including brittle materials.
Last modified: