Nondenstructive testing
Brilliant perspective: Computer tomography analyzes damage to raw materials under load
The ability to test various materials without destroying them is essential in many areas of commerce and industry. The Fraunhofer Institute for Structural Durability and System Reliability LBF has now developed a new method that for the first time combines the mechanical testing of a component under realistic loads with a radiographic examination. The method is used to characterize materials, and it makes it easier to assess inclusions or damage to raw material with regard to their influence on the durability and service life. In so doing, Fraunhofer LBF provides materials designers and manufacturers as well as scientists with information for better understanding of material behavior and material characterization.
New method combines mechanical testing of a component under realistic loads with a radiographic examination
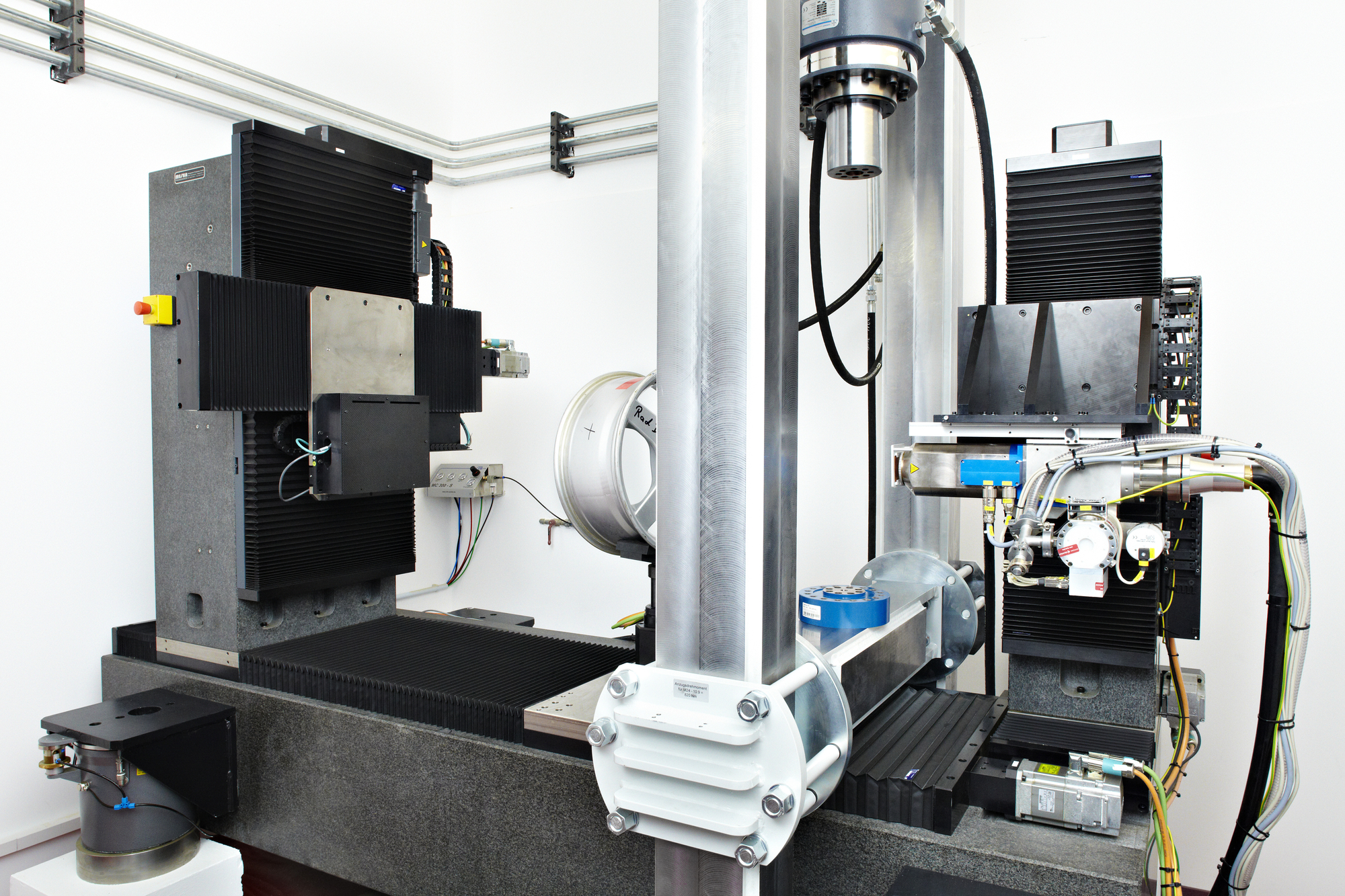
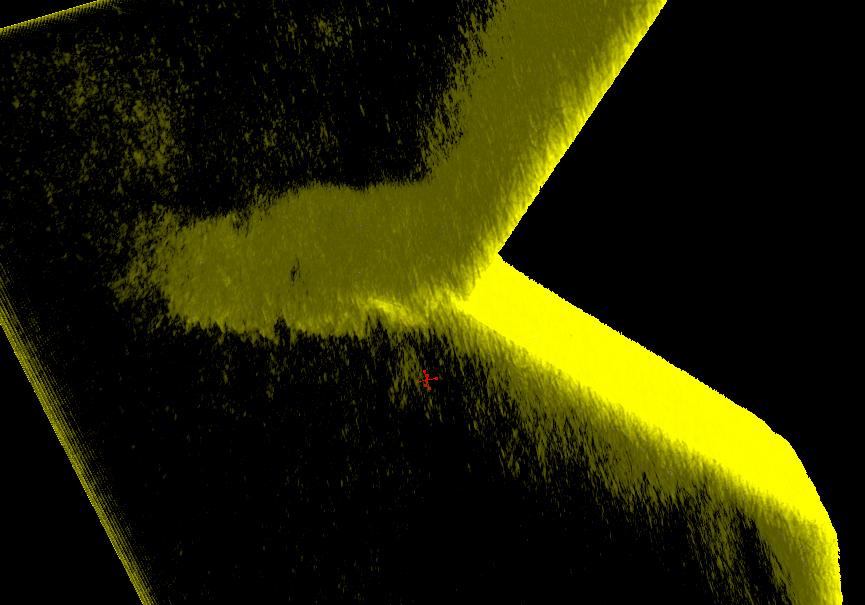
“Understanding how damage occurs to the material of a component while is placed under realistic mechanical loads is one of the key questions in materials science, and was previously not possible,” emphasizes Oliver Schwarzhaupt, scientific employee in Function-Integrated Lightweight Construction at Fraunhofer LBF. With the new test method, the tested component remains in the x-ray equipment during the mechanical load. As a result, the exact location in the material can be observed and analyzed throughout the entire load duration. The previous concepts were never able to achieve the necessary precision of just a few micrometers with the alternating insertion and removal of the sample with intermittent radiological examination. “The new process represents a huge advance in regards to detail resolution and precision, as well as the retrievability of possible causes of damage,” explains Schwarzhaupt.
While the scientists from Darmstadt are subjecting the component to a mechanically dynamic service life load, they can use the radiological examination in this cycle to observe and illustrate the occurrence and progress of the damage. With forces in the test machine of up to 250 kilonewtons, even high-strength components made of carbon fiber like those used in aircraft construction can be examined. “There is still a great need for examination to understand the failure mechanisms in carbon fiber-reinforced plastics,” adds Schwarzhaupt.
With the most modern imaging processes, cracks and damage in material can be illustrated vividly and in three dimensions, opening up many possibilities for analysis. With the use of a microfusion pipe, the x-ray equipment in the Fraunhofer LBF has a high resolution capacity of just a few micrometers. In this way it is possible to detect the smallest signs of damage even as it begins to occur, or determine that the slightest irregularities in the material are the point of origin for the damage. In the area of fiber-reinforced plastics in particular, the occurrence of damage on the fiber level can be studied.
With this knowledge about the cause of the error and the error sequence, developers, designers, and manufacturers can now improve their materials, components, and manufacturing processes even before a crack is macroscopically visible. “Our new concept makes a great contribution on the topic of material understanding and is clearly better able to meet customer-specific requirements in the area of material failures at an early stage,” ensures Schwarzhaupt.
Last modified: