Circular economy, quality control, online-Seminar / 2025
Constant optimization of materials and products made from polyolefin recyclates for sustainable solutions
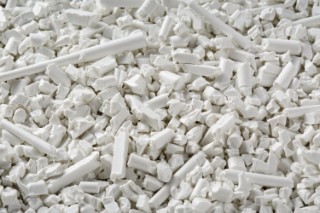
To ensure the quality of recyclates, the Fraunhofer Institute for Structural Durability and System Reliability LBF is planning a new joint research project with partners from industry to optimize polyolefin recyclates for sustainable solutions. New analytical methods and user-friendly evaluation strategies should enable cost-efficient quality control and improvement of recycling processes. The project promotes the transformation into a circular economy and invites partners to collaborate. More information will be provided in a free online seminar on May 6, 2025.
more info