Improved methods for failure prediction of hard foam components
For optimal modelling of material properties of hard foam in FEM simulations, hydrostatic tension and compression tests are of crucial importance. These tests are essential during design to ensure that the material will not fail in the application. Researchers at Fraunhofer Institute for Structural Durability and System Reliability LBF have developed innovative test procedures and improved methods for the safe design of hard foam components.
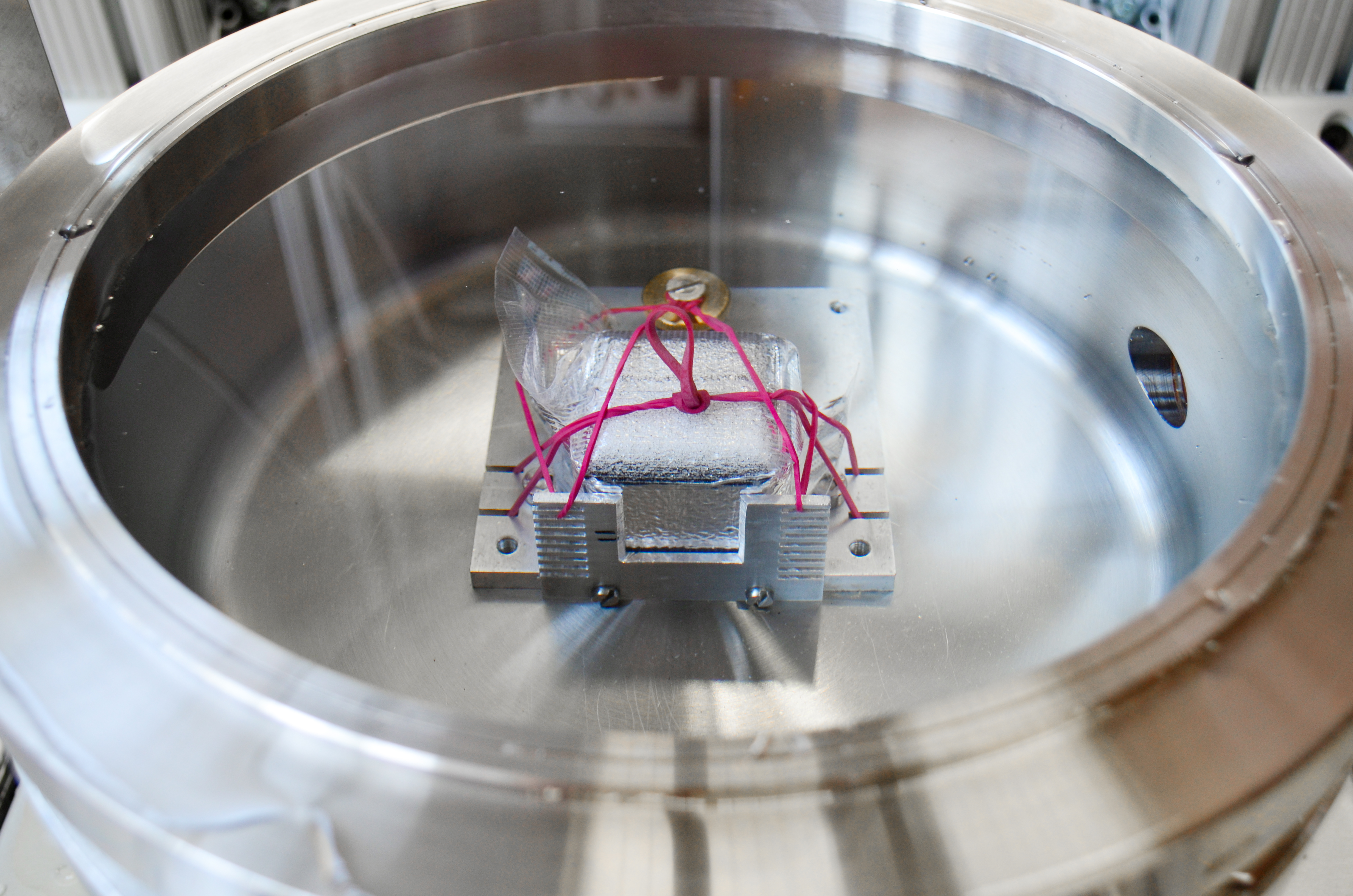
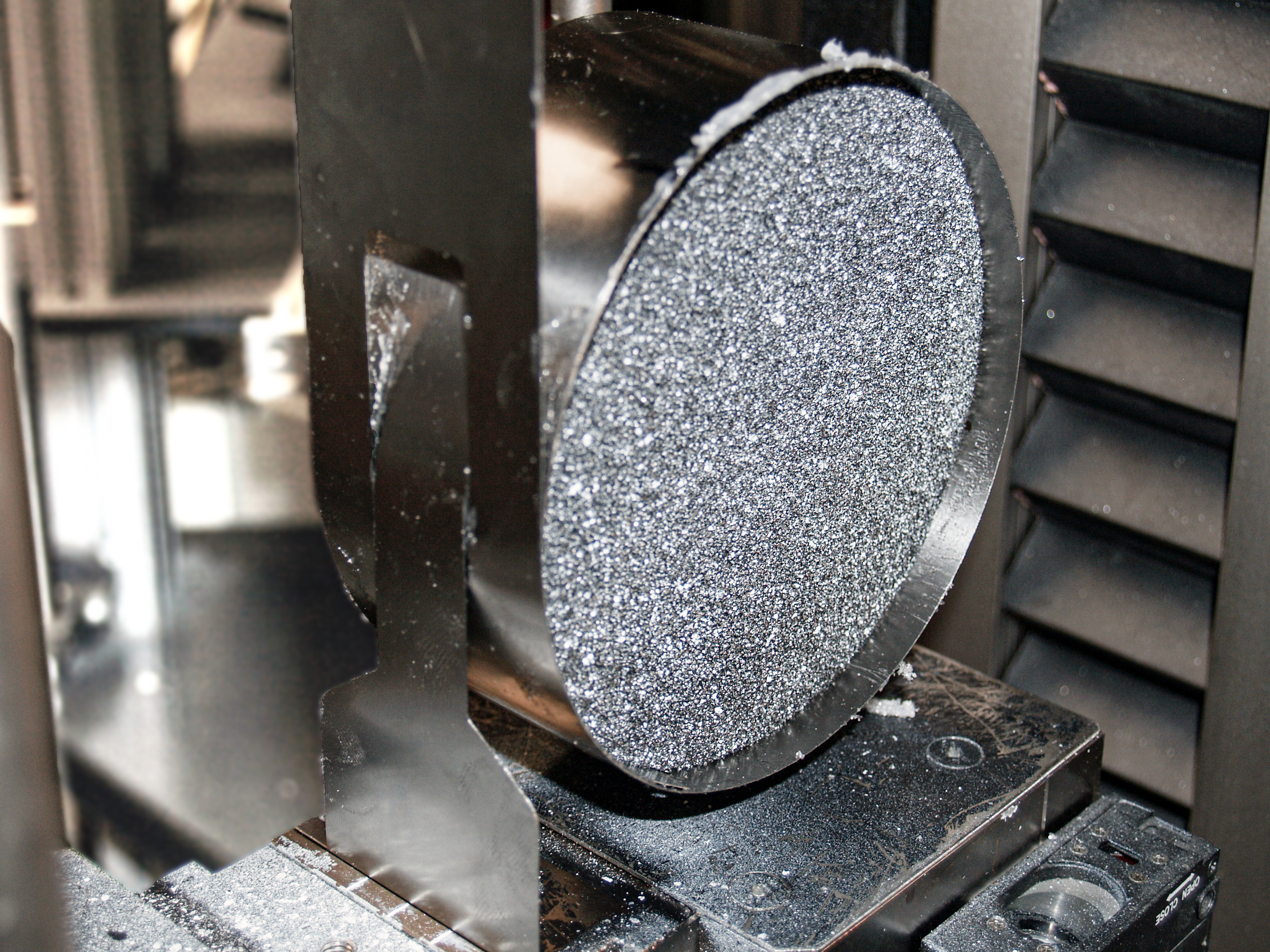
Nowadays, a universally accepted procedure for multiaxial tests of hard foam components is missing. Some loading cases can hardly be realized experimentally. For example, plausible specifications for a hydrostatic tensile test are unknown and the balanced biaxial tensile test is costly to perform. To handle these problems, experts at the Fraunhofer Institute for Structural Durability and System Reliability LBF have established 2D and 3D balanced compression tests. The results of these experiments are clear and easy to interpret. In addition with uniaxial tensile, compression, and torsion test, these test data ensures reliable modelling and plausible extrapolations, which allow for the estimation of the unavailable hydrostatic tensile data.
Novel 2D compression test
The equibiaxial compression loading is realized in a conventional tensile testing machine, applying a circular disc as specimen and a sheet steel loop for load application. The resulting effort is comparable to standard tensile tests. The 2D compression test represents an effective method for the first estimation of material behavior. However, for precise modelling a hydrostatic compression test is essential.
Hydrostatic loads for reliable failure analysis
Two types of material behavior under hydrostatic compression should be distinguished: destruction of the cells and hydrostatic collapse of the overall structure. Scientists at Fraunhofer LBF have implemented an innovative method for the testing of material behavior under hydrostatic compression and applied it to several polymeric hard foams. They offer support on every level of the design process. As a result, the reliable solutions for optimized structures were achieved.
For reliable modelling of materials, which fail under hydrostatic compression (hard polymeric and ceramic foams, aerated concrete, soil, sintered and granular materials, etc.), the hydrostatic compression test is mandatory. The material properties from this test cannot be calculated from the tensile, compression, and torsion test data. Possible extrapolations, such as given above by the 2D compression test, may provide only estimates and should not be applied for critical applications.
The hydrostatic (balanced 3D compression) test provides the necessary information for modelling of the elastic behavior and failure at multiaxial compressive loadings. The results of the hydrostatic test lead directly to the required material model parameters, simplifying the fitting procedure significantly. Among others, the bulk modulus of the elastic behavior is a result of these experiments.
New method suitable for further materials
With the new method, components containing hard foams can be designed more reliably and more cost-effectively. It allows to take safe decisions about the choice of material for specific applications. “Unexpected cases of failure” in the application can be ruled out. The method also seems very promising for further materials like ceramic foams, aerated concrete, soil, sintered and granular materials, etc.
Last modified: