Identification of damage using a multidisciplinary assistance system
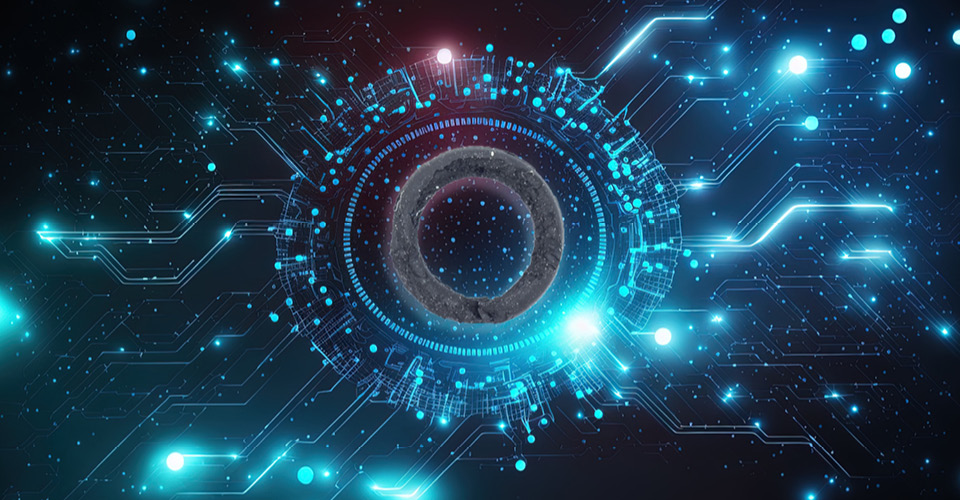
Due to the wide variety of damage patterns on elastomer components, it is not always easy to trace the cause of the damage. The Fraunhofer internal project “AI-based
damage analysis of technical elastomers – KISTE” discusses the possibilities of objectively evaluating damage cases using artificial intelligence. The resulting process, using simple components as an example, can be transferred to customer-specific applications.
Elastomers are subject to extremely high and complex requirements, such as mechanical and thermal loads and various media influences. Damage to these components can result from these loads as well as from aging, deviations in the manufacturing process, and other factors. An analysis of damage to components can be carried out with the help of VDI 3822.
However, experience and expertise, as well as similar damage patterns with different causes, lead to a subjective assessment of damage in this process. The KISTE project automates and objectifies this time-consuming and costly process and explores the necessary framework conditions (e.g., input parameters, training database, extrapolation potential, etc.) for practical implementation.
The first group step toward objectively evaluating the causes of damage to elastomers in a process chain has been successfully implemented. The initial focus was on investigating the required database. Since there are typically not enough damaged parts available to train an AI model, synthetically generated damage data was created and various data augmentation methods, such as geometric transformations and color changes, were investigated and applied to determine their effectiveness. This allows a representative number of damage images for different causes of damage to be created, the process requirements to be systematically explored, and the robustness of the model approach to be increased.
In a second step, the process chain is expanded from a classification model based purely on image data to a multi-stage, multimodal classification model. For this purpose, additional scalar input parameters (e.g., material properties) are added to increase the accuracy of damage determination and make the classification process more robust overall. Another research question will relate to the extrapolability of the process chain to damage examples outside the training data set of the AI models. This will also be optimized for future follow-up projects, for example through transfer learning approaches.