Artificial intelligence, vibration mitigation, vibration reduction, genetic algorithms
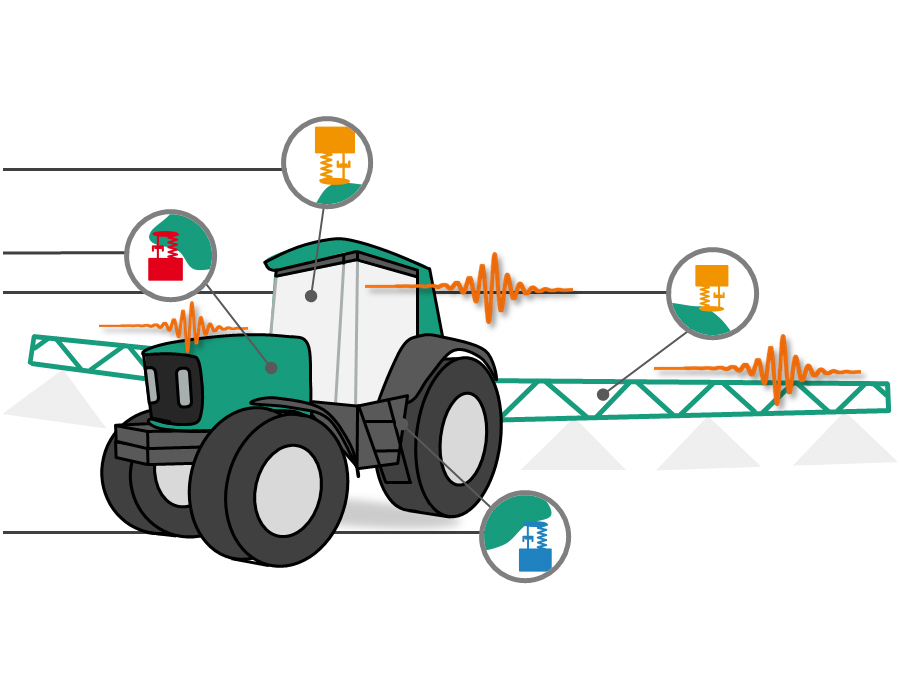
In order to prevent disruptive or process-critical vibrations, additional vibration control measures such as vibration absorbers, inertial mass actuators or damping measures are often used. However, especially in distributed systems, conventional optimization methods reach their limits due to the interactions of the various effects with each other. Having amassed many years of experience, Fraunhofer LBF scientists are able to solve vibration technology problems, from the use of experimental or numerical analysis to the implementation of suitable measures. The use of artificial intelligence now offers the possibility of reaching the best solutions even faster. Companies that have vibration-related problems with vibrations, noise or shaking on machines can obtain a complete solution from Fraunhofer LBF – from an analysis of the problem to solving it.
The following application example shows how this can be achieved: In machines for machining large components, the workpiece mass has a significant influence on the dynamic behavior of the machine. Additional vibration control measures such as absorbers, neutralizers or damping components are often implemented to prevent disruptive vibrations that affect component quality. As a rule, these measures must be precisely matched to the structure to be stabilized or the excitation. If this changes, for example due to the use of workpieces of different mass, the tuning must be adjusted. Artificial intelligence, together with adaptive vibration technology measures, can effectively meet this challenge.
If a machine is equipped with a number of vibration technology measures, for example adaptive absorbers or machine bearings, the pre-equipped measures can be optimally adjusted using the developed AI algorithm using a reduced model of the machine and knowledge of the workpiece that is to be machined. This allows the highest possible part quality to be achieved from the very first workpiece. Fraunhofer LBF has implemented various adaptive absorbers and machine bearings to achieve the automated adjustment of vibration control measures.
Fraunhofer LBF's complete solutions are based on evolutionary algorithms and allow solutions to be found quickly and automatically. They are based on an expandable library with various passive, semi-active and active measures, which can also be used in combination with each other.