thermal conductivity, thermal insulation, heat storage
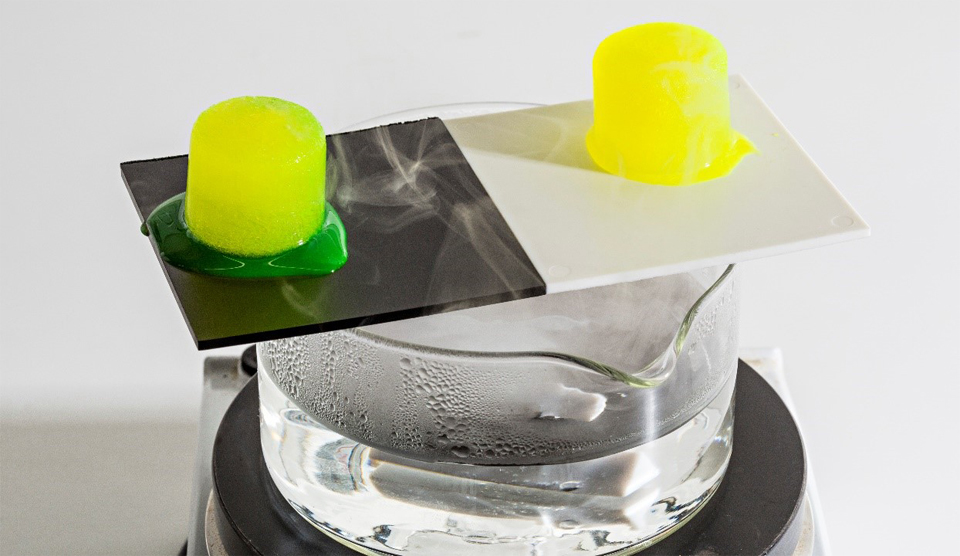
New challenges are rising for thermal management in relation to e-mobility. The primary influences on the range of electric vehicles are the traction battery and the drive system. However, on a secondary level, the temperature-dependent performance of the battery and the energy savings in the auxiliaries, e.g. air conditioning in passenger compartment, are decisive. For the latter issues, the phase change materials play an important role in mitigating the effects of peaks in temperature.
Phase change materials store a large part of the energy supplied to them in the form of latent heat, e.g. for a phase change from a solid to a gel-like or liquid state. These functional materials are increasingly being used in the thermal management of electric vehicles.
In this context, a range of requirements must be met. In addition to keeping weight as low as possible, high enthalpies during the change in thermodynamic state in the desired temperature window (often in the range of 5 – 25°C) are necessary. Due to their high enthalpies of melting and crystallization, paraffins now find particular use here. Making sure to prevent any leakage of paraffin is very important in order for the safe use of these phase change materials.
In the EU DOMUS project, new, dimensionally-stabilized phase change materials were developed based on thermoplastic styrene block copolymers (SEBS and SEEPS). These are set apart by the fact they can absorb larger volumes of paraffin (in this case, for hexadecane up to 90 wt%) than, for instance, polylefins (up to max. approx. 75 – 80 wt.%). At Fraunhofer LBF, the first step was to establish the structure-property relationships within the system. The materials were then optimized on the basis of this. As a result, it was possible to achieve enthalpies of up to 195 J/g with high thermo-mechanical dimensional stability. The leakage behavior, which takes the form of a loss of mass at higher temperatures, can be minimized through the targeted adjustment of the molecular structure. Dimensionally-stabilized plates were then produced from these materials using hot pressing. Macro-encapsulation with paraffin makes it possible to create functional pads using impermeable barrier films that show almost no leakage of paraffin under laboratory conditions. As part of the ongoing DOMUS project, the materials developed at Fraunhofer LBF were integrated at HUTCHINSON, our development partner, in the headliner of a vehicle (see Figures 1 and 2). Our project partner is subjecting these to comprehensive evaluation in relation to their target application in cars.
As part of another EU project (SELFIE), together with consortium partners, a Fiat Doblo that was originally developed for an internal combustion engine drive system is being retrofitted with an electric drive system suitable for series production. A thermal management system is also being developed and built here. This involves ensuring optimal thermal management of the traction batteries at different states of charge. The coordination of the constructive implementation is one of Fraunhofer LBF’s main tasks.
The following figure shows the structure of the traction battery. Here, a highly rigid, lightweight and flame retardant composite housing, which was built at Fraunhofer LBF is used. This battery housing is equipped with battery cells that can be actively cooled using the cooling plates installed. Aluminum based modules are also used. The core of this module is made from aluminum foam, which is in turn loaded with a phase change material. The phase change material makes it possible to mitigate the effects of peaks in temperature that occur during the rapid charging process, which can achieve charging rates of up to 6C (i.e. six times the rated capacity). The combination of insulating housing and liquid cooling allows for the PCM material to be reactivated following a rapid charging process and the cell temperature to be influenced in a targeted manner.
The entire traction battery is built, integrated in the Fiat Doblo and its performance demonstrated as part of the project.
Both projects were funded as part of the Horizon 2020 EU research and innovation program (grant agreement no. DOMUS: 769902, SELFIE: 824290)