electromobility, cost efficient lightweight design, battery system
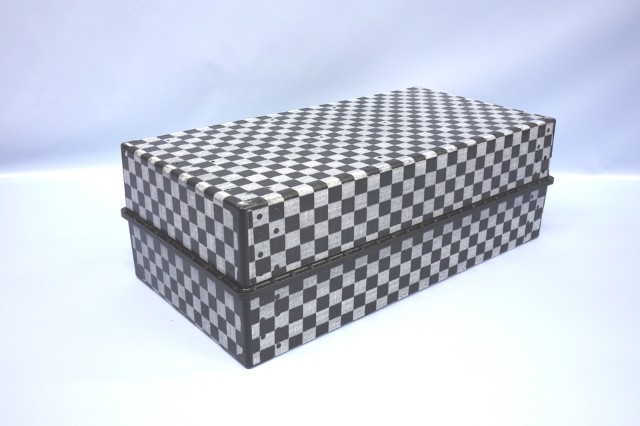
Several car manufacturers have taken up this challenge and successfully reduced vehicle weight with the help of lightweight composite construction. However, the cost efficiency of fibre composites and manufacturing processes is still a fundamental problem in automotive lightweight construction. New classes of materials based on continuous fibre-reinforced thermoplastics (CFRTP) and novel hybrid manufacturing processes, however, enable new approaches, especially with regard to cost-efficient lightweight construction in electromobility.
A team of researchers from Fraunhofer LBF have applied their expertise in this field to produce a lightweight battery housing from continuous-fiber-reinforced thermoplastics in a three-dimensional (3D) sandwich design, using an innovative process that combines high-efficiency foam injection molding with CFRTP.
The so-called in-situ CFRTP sandwich process is used, thus enabling the production of finished lightweight battery housings within two minutes without the need for post-processing. In addition, functions such as thermal insulation capability or flame resistance can be integrated in the same process step.
The housing structure consists of two CFRTP cover layers and a connecting integral foam structure in between. The cover layers consist of unidirectional tapes, which are first woven creating a cross-ply layup and then consolidated, resulting in the striking checkerboard appearance. The laminate resulting from this process step is then 3D preformed and both sides inserted into a specially-developed hybrid foam injection mold. The controlled injection of an integral foam between the laminates in this way creates the three-dimensional structure of the housing with fiber composite cover layers and a foam core. The bonding of the CFRTP cover layers and foam core, which is of fundamental importance to the load-bearing capacity of the sandwich structure, is achieved in-situ during injection.
The stress-equivalent sandwich design results in the highest weight-specific mechanical properties, while at the same time reducing the material consumption of the fiber composite laminates used as the latter are only applied in highly stressed areas. The low component costs are hence achieved through the resulting reduction in material costs, in combination with the very short cycle times of the in-situ CFRTP sandwich process.
The required mechanical properties were verified by finite element simulations during the design phase and were validated under real conditions on the testing bench (ISO 12405-2, 12405-3).
The project was funded by the European Commission as part of the H2020 funding program (H2020-GV-2016-2017/H2020-GV-2017).