DLC coatings, elastomers, seals, tribology
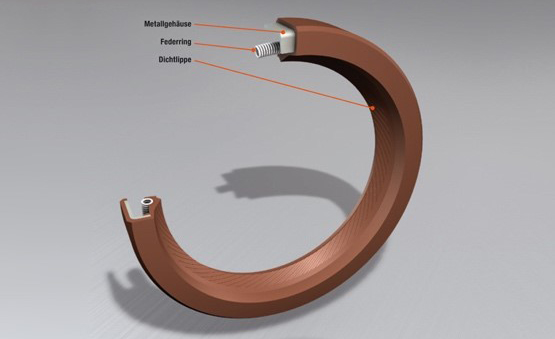
The aim of the project was to create robust, abrasion-resistant coatings on a wide range of substrates, such as elastomers and thermoplastics. Coatings such as this are particularly interesting when used on the surface of seals, which are subject to constant friction and rubbing, as is the case for the radial shaft sealing rings mentioned above. A range of approaches for improving the abrasion resistance of DLC-coated materials used in sealing applications were investigated, in cooperation with Fraunhofer IVM (which has been applying the DLC coatings to the test piece and carrying out the tribological tests), Fraunhofer ILT (which has been looking at how a surface structure influences the DLC coating) and Fraunhofer IAP (which has been discovering new approaches in relation to adaptive seals). The focus of Fraunhofer LBF is on developing the formula for the base material, which can be used in a targeted manner to produce structures and properties with improved resistance. For the area of elastomers, robust DLC coatings were applied to test pieces made from nitrile rubber (NBR) or fluorine rubber (FKM). The mechanical properties of the elastomeric test pieces created in this way were measured cyclically and statically by Fraunhofer LBF. Here, it was demonstrated that the coatings were homogeneous and robust. The characteristic curve of the test piece differs only slightly from the non-coated test pieces.
The cyclic measurement of the service life also shows that the coated test pieces can withstand the requirements better than the non-coated test pieces. A direct comparison shows that the number of life cycles of the test pieces before and after application are roughly the same.
To gain information in relation to the chemical structure of the DLC sheets, analysis using Raman microscopy were conducted. This makes it possible to distinguish between crystalline and amorphous portions of the DLC layer and to determine the local distribution of both portions as well as the roughness of the DLC layer. When comparing DLC coatings on different substrates, e.g. of differing levels of hardness, this allows us to make statements about the uniform distribution of the layer and adhesion of the layer. Moreover, it is possible to draw conclusions about the wear on the DLC layer from a comparison of probes, which were subjected to different levels of friction in tribological tests.
The effect of the DLC coating on tribological properties was investigated at Fraunhofer IWM using a ring on disc tribometer. It was found that surface wear of all the materials tested was significantly reduced by the DLC coating. However, the effect of the DLC layer differed depending on the properties of the substrate, such as the level of hardness.