Sensor-based condition monitoring of automotive hydrogen pressure vessels made of FKV
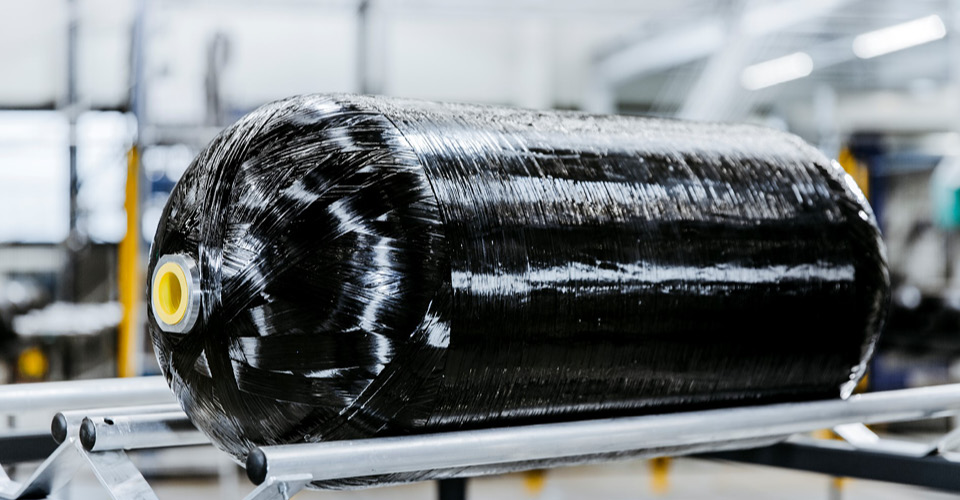
As highly stressed safety components, pressure tanks for the storage of gaseous fuel represent a core element of H2 propulsion systems for motor vehicles. Tanks made of fiber-reinforced plastics have a significantly lower mass than pure metal tanks with the same working pressure [1]. This makes them attractive for use in the mobility and transportation sector. They are designed for a fatigue life of up to 20 years at operating pressures of 200 to 1000 bar [2].
The visual inspection of tanks in automotive applications, which is currently prescribed at intervals of two years, is a purely external assessment that hardly allows any conclusions to be drawn about the condition inside the thick-walled fiber composite. On the one hand, "overly" conservative complaints, which may result in the unnecessary replacement of tanks that are actually still functional, can lead to high repair costs. On the other hand, a false assessment of a defective tank as "safe" must of course be ruled out under all circumstances.
The aim of the project is to objectify the evaluation based on structural health monitoring (SHM) data by on-board structural monitoring of pressure vessels using suitable sensors and evaluation electronics and to enable permanent monitoring in H2 fuel cell vehicles (H2-FCEV) in the future. In addition to the use of SHM data for repairs and servicing, it will also be possible in the future to initiate targeted measures for safe vehicle recovery during rescue operations in the event of vehicle accidents or misuse.
As part of the project, Fraunhofer LBF is working closely with the research partners. Together with them, a methodology for the application of fiber-optic and piezoelectric sensors to fiber composite pressure vessels is being further developed. The fiber-optic strain sensors are capable of measuring the material stresses in the fiber laminate. The piezoelectric sensors are used to detect the ultrasonic noise that occurs when the matrix or individual fibers of the laminate fail as a result of impact damage or overstressing. Using samples of the material, the damage to the material is first artificially created in the laboratory, detected with the sensors, and then classified based on the signal signatures. The sensor and application technology developed will be transferred to the application on FKV high-pressure tanks and validated in burst, fatigue and impact tests.
Key areas of focus at the Fraunhofer LBF include the development of a signal analysis procedure based on the acoustic emission method to distinguish between different material-typical damage mechanisms and a calculation methodology for the fatigue behavior of the fiber composite. Finally, based on its existing experience in the field of driving measurements, the institute supports the integration of the container monitoring system into the electrical, electronic and information technology environment of the vehicle.
Overall, the automated metrological monitoring of the pressure vessels promises a further increase in the safety level. At the same time, high costs due to the unnecessary replacement of tanks that are still functional are avoided. In addition, the sensor technology enables cost-effective and efficient monitoring of the production quality. Accompanying monitoring allows more information to be gained during product development, which contributes to a reduction in development and testing times.
Funding code: 03B11021E
Joint project: NIP II - HyMon
Funding source: Federal Ministry of Digital Affairs and Transport ()
Project executing organization: Forschungszentrum Jülich GmbH (PT-J.EVI1)
Support program: Energy