Innovative structural concepts for lightweight, efficient vehicles without compromising on comfort or performance
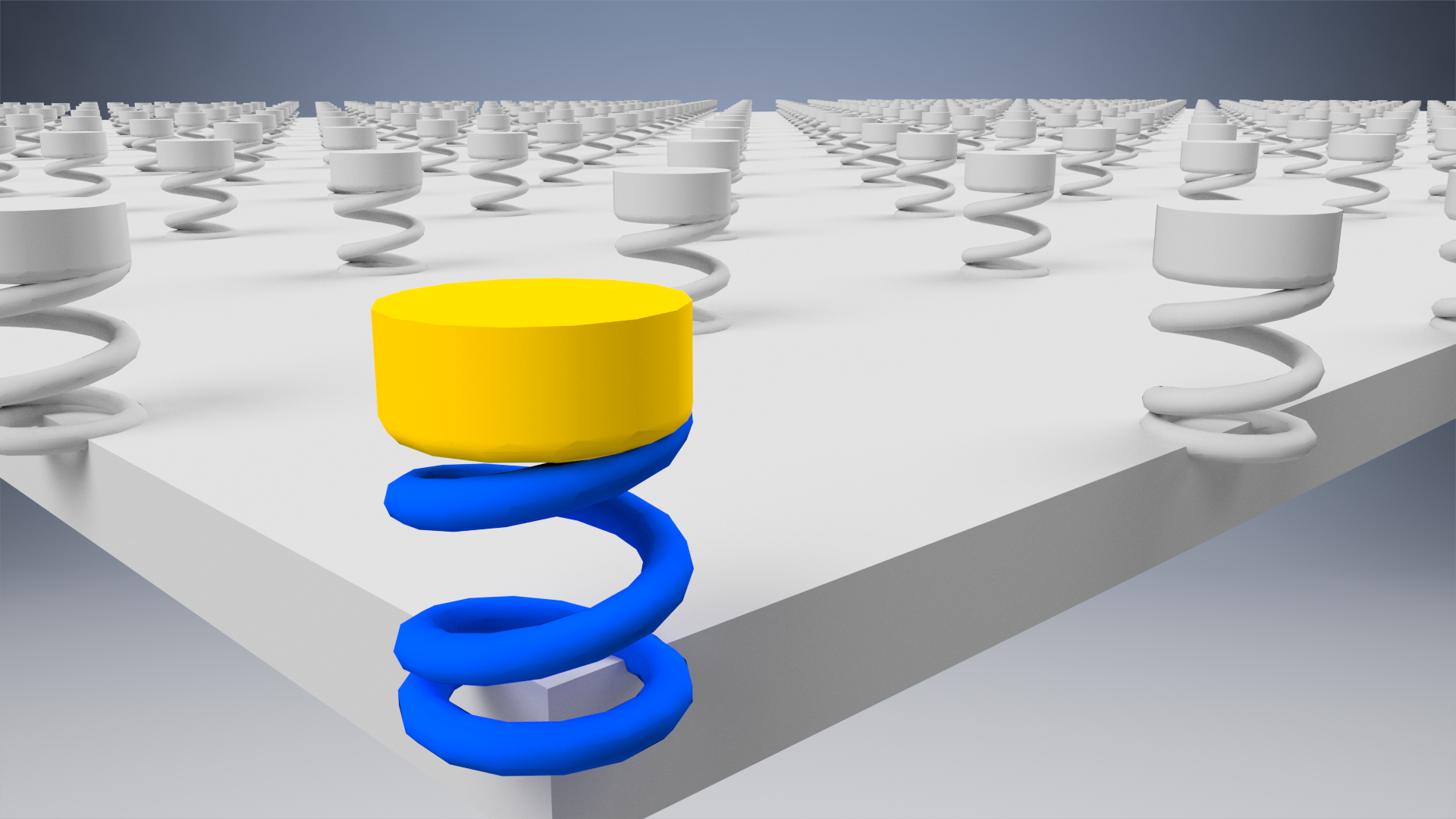
Vibro-acoustic metamaterials consist of a regular spatial arrangement of identical, very small, mechanical resonators. This structure allows them to greatly reduce vibrations in a predetermined frequency range with minimal additional weight, eliminating the trade-off between very slim-line structures and optimal comfort. Compared with conventional measures, this composite material achieves significantly greater and broader-band sound and vibration reduction.
Due to the small-scale nature of the unit cells, vibro-acoustic metamaterials can be easily integrated with a high degree of design freedom and can comply with static, vehicle dynamic and crash-relevant design requirements that are crucial in automotive engineering. Compared to active systems, vibro-acoustic metamaterials require no additional energy and are estimated to be significantly less expensive. The geometry and size of the unit cell depends on the application and targeted frequency range. The application-specific design concepts, design processes and production methods required for use in vehicle construction are being developed in the “viaMeta” research project.
The work at Fraunhofer LBF is based on the existing scientific expertise at the institute in the field of material development and vibro-acoustic metamaterials. This knowledge is being used to develop a design system for the metamaterials and to describe the structure and modes of action of the metamaterials. Modeling methods such as the finite element method and novel, data-based AI methods are used to simulate and optimize the behavior of the metamaterial components in a virtual vehicle prototype. The virtually optimized concepts are produced as real demonstrators in order to prove the savings potential and effect on comfort in the real vehicle.
Funded by the Federal Ministry for Economic Affairs and Energy (BMWi) on the basis of a resolution of the German Federal Parliament (Bundestag).
Project partners involved in the “viaMeta” research project include Mercedes-Benz AG, BOGE Elastmetall GmbH, Novicos GmbH, Institute for Automotive Engineering RWTH Aachen University (IKA) and Fraunhofer Institute for Structural Durability and System Reliability LBF.