New manufacturing processes and materials
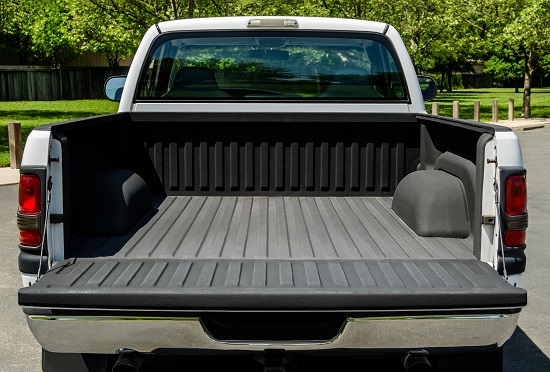
Project »ECO2-LInE«
In the research project, 10 partners will use the high-speed additive manufacturing process known as SEAM (screw extrusion additive manufacturing) to develop large components made of sustainable natural fiber-reinforced plastics for various cross-industry applications. In order to make the best possible use of the lightweight potential, the design takes into account the process-dependent material and component properties.
In the research project, 10 partners will use the high-speed additive manufacturing process known as SEAM (screw extrusion additive manufacturing) to develop large components made of sustainable natural fiber-reinforced plastics for various cross-industry applications. In order to make the best possible use of the lightweight potential, the design takes into account the process-dependent material and component properties.
The CO2 reduction aspect is achieved not only by targeted weight reduction through the use of sustainable lightweight materials in new designs, but also by a systematic review and adaptation of the entire production chain, taking into account resource efficiency and minimization of greenhouse gas emissions. The Fraunhofer Institute for Machine Tools and Forming Technology IWU is responsible for the development of the 3D printing process in cooperation with S.K.M. Informatik GmbH. The Fraunhofer Institute for Structural Durability and System Reliability LBF is primarily responsible for the development of the materials.
The project aims to achieve sustainability and resource conservation, automation and digital networking, cost-effectiveness and increased productivity, as well as transfer principles for industrial production, such as industrial qualification of the additive SEAM process through development and testing for specific demonstrator partner applications.
The demonstrators developed in the project - a sustainable bench, lightweight seats, pickup attachments and a novel frame element for rail vehicle transfer systems - will also be tested for their suitability for use in series production. Their suitability for series production will be demonstrated in mechanical strength tests. The Fraunhofer LBF will contribute its expertise in lightweight construction, prototyping and the holistic evaluation and analysis of materials, components and systems. Among other things, the scientists will investigate the vibration dynamics of the new seats and implement flame protection for the frame elements by developing customized additives.
Once the project has been successfully completed, the participating users will be able to market the sustainably manufactured natural fiber-reinforced components, expand their production and thus secure jobs in Germany. The new construction methods will offer their customers numerous advantages in terms of weight reduction, energy savings, greenhouse gas emission reduction and durability.
The project "Saving CO2 through the use of new manufacturing processes and materials for the development of sustainable lightweight components for interior and exterior applications", in short: ECO2-LInE, was launched in May 2021 and is funded by the Technology Transfer Program for Lightweight Construction of the Federal Ministry for Economic Affairs and Energy. Under the leadership of Martin Schnierle, CEO of Hermann Schnierle GmbH, a total of ten partners from research and industry will work together over a period of three years.
The Fraunhofer LBF is primarily responsible for material development, while the Fraunhofer IWU is responsible for developing the 3D printing process in collaboration with S.K.M. Informatik GmbH, which is responsible for programming the printer software in the project. The users of the sustainably manufactured natural fiber-reinforced components in this project are Hermann Schnierle GmbH (sustainable bench and lightweight seats), FiftyTen (pickup attachments) and Hübner GmbH & Co. KG (new frame elements for rail vehicle transition systems). The companies Biowert Industrie GmbH, J. RETTENMAIER & SÖHNE GmbH + Co KG, 3M Deutschland GmbH and METROM Mechatronische Maschinen GmbH are involved as associated partners.