Use of vibro-acoustic metamaterials to reduce vibrations in upper stages of launchers
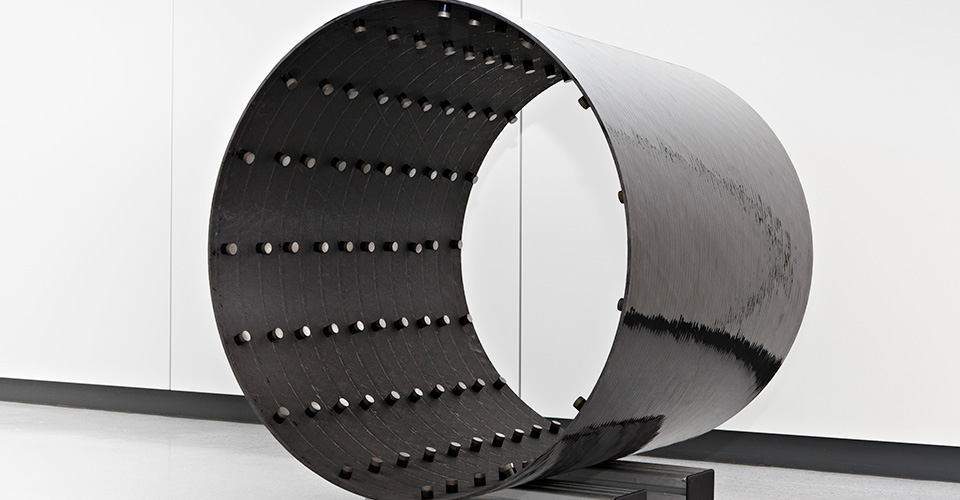
To remain competitive, all design and operational aspects of space launchers must be fully optimized. One of these aspects is lightweight construction for rocket components, which is why metallic materials are increasingly being replaced with fiber-plastic composites. However, this is accompanied by increased vibration loads, especially during the launch phase, which can lead to damage to the structure and payload.
Researchers working on the “Silent Running” project (German Aerospace Center INNOspace Masters Challenge) at Fraunhofer LBF investigated the use of vibro-acoustic metamaterials to reduce structural vibrations on space launcher components. Vibro-acoustic metamaterials are specially designed structures consisting of a number of periodic mechanical resonators applied to the target component. The interaction of the local resonances with the basic structure when subjected to loads during the rocket launch enables efficient vibration reduction in the defined frequency range. This frequency range is referred to as the stop band and represents the main advantage over conventional vibration reduction measures, such as dampers.
The use of vibro-acoustic metamaterials is demonstrated in the project on a cylindrical component representing, for example, the upper stage of a launcher. For this purpose, a scaled cylindrical structure made of fiber-plastic composite with vibro-acoustic metamaterials in a differential design (i.e., resonators are additionally applied to the target structure) is used as the final demonstrator. The stop band should be in the range of around 100 Hz. However, a broader-band vibration reduction in the range up to 500 Hz is also desirable due to complex excitation profiles. Furthermore, the additional mass resulting from the vibration reduction measure must not exceed 18 percent relative to the reference structure.
The development steps include concept design of individual resonators, validation at the resonator level, implementation as a composite and the selection of the best version for the final demonstrator (see Fig. 1).
Three concepts were developed and experimentally investigated with regard to the relevant requirements (see Fig. 2). The need for low resonator frequency and high damping properties led to the selection of soft elastic materials.
As all concepts succeeded in achieving the desired vibration behavior, the favored concept was selected for implementation on the final demonstrator using the following criteria:
The selected concept is a rod resonator. The spring element of the resonator is a hollow cylinder made of polyurethane and the mass element is a solid cylinder made of steel. The scaled launcher component is represented by a cylinder in the dimensions with a wall thickness of . A total of 150 resonators were used on this component and experimentally characterized (see Fig. 3).
As can be seen in Fig. 3, the vibrations could be reduced by factors up to 60 dB within the range of 100 to approx. 200 Hz. A broad-band damping behavior was observed in the frequency range up to 600 Hz. This confirms the effectiveness of the concept and demonstrates the high potential of vibro-acoustic metamaterials for space travel structures.