Secure bonded joints in highly stressed hybrid structural components
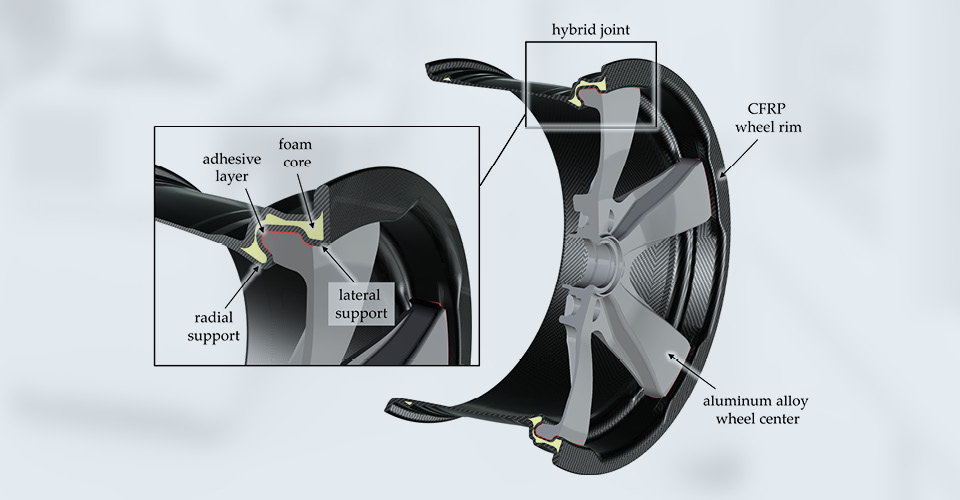
Already established on the market are hybrid wheels consisting of an alloyed aluminum star and a wheel rim made of carbon fiber composite. The connection between the two joining partners is usually realized by a bolted joint, as high structural and thermal loads prevail in the joint. However, the realization of the bolted joint is very complex, as mechanical machining of the fiber composite joining partner and the integration of threaded holes in the aluminum joining partner as well as sealing measures are required. Furthermore, the bolted joints are usually designed with a positive sleeve construction to counteract resulting shear forces. These additional elements lead to a compromise in terms of lightweight construction.
For joining metal and fiber composite parts, structural adhesive joints generally offer several advantages: The load introduction into the fiber composite part can be realized without damaging the fiber structures. Dimensional deviations of the joining partners can be compensated (to a limited extent) by the respective adhesive thickness, if necessary, and the total mass of the joint can be reduced compared to a bolted joint.
As part of the publicly funded GOHybrid research project, a bonded joint for a hybrid wheel was developed together with the consortium partners to demonstrate its performance and lightweight potential. In this context, the wheel as a safety component must exhibit reliable resistance to high structural loads that occur under various load conditions such as straight-ahead driving, cornering, acceleration and braking. Furthermore, the individual materials of the hybrid bonded joint must be able to withstand both low and elevated temperatures and compensate for their different thermal expansions.
At Fraunhofer LBF, the focus was on the development of design solutions for the hybrid connection and experimental investigations. The joint developed combines the adhesive bonded joint with a form-fit geometry and still enables a joining process of the wheel spider in the direction of rotation. In addition, the thermal residual stresses in the joint were significantly reduced by adapting the fiber structure in the rim area. To validate the developed design solution, component-like specimens representing the connection of an aluminum spoke to the composite rim were developed, fabricated and tested at different temperatures and load cases. The test results show sufficient strength of the bonded joint as well as an improvement of the developed form-fit joint compared to a simple bonded joint.
The GOHybrid project - Design and optimization of hybrid joints with special consideration of the different thermal expansions of the material partners - was funded by the German Federal Ministry of Education and Research as part of the HyMat materials platform.
In addition to the Fraunhofer LBF, participants in the GOHybrid project include