Identification and optimization of welding parameters
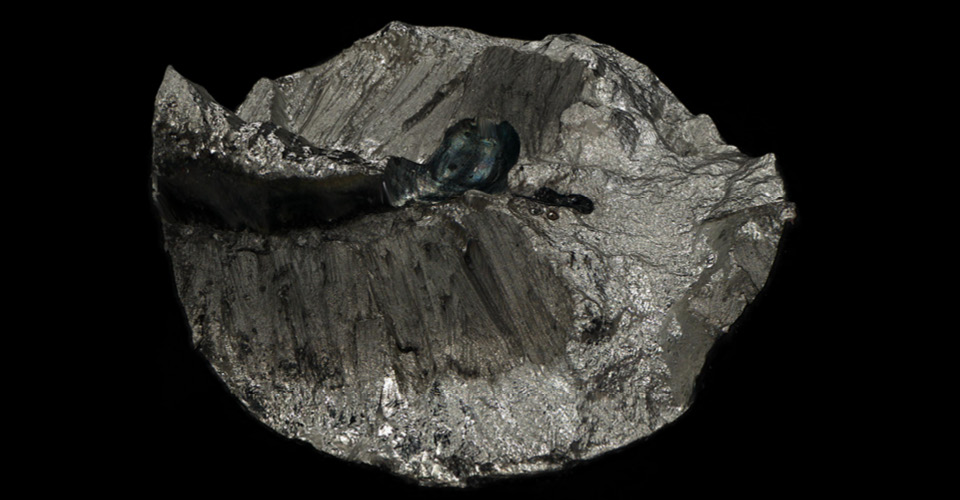
In the present research project "nodularWeld", both the weldability and its influence on the fatigue behavior were investigated for three different cast iron alloys relevant in the large castings sector. Due to the different microstructural characteristics of these casting alloys - EN-GJS-400-18-LT (ferritic microstructure), EN-GJS-450-18 (ferritic solid solution strengthened microstructure) and EN-GJS-700-2 (pearlitic microstructure) - the suitable welding parameters had to be worked out in a first step on the basis of preliminary welding tests. Quasistatic and metallographic examinations were used to evaluate the weldability of the dissimilar weld. After identification of the filler metals and the welding parameters for satisfactory strength behavior, thick-walled cast plates with dimensions of 1000 x 600 x 150 mm were cast for the main test series in the first step, then machined, and in the last step the repair weld was produced.
As part of this main series of tests, small round specimens from the base material, the heat-affected zones and the weld metal were first investigated under strain control and axial loading to determine the cyclic material properties of these three material zones. Both the stress-based and strain-based cyclic material behavior were determined through investigations on integral round specimens exhibiting all three zones of the welded joint. Based on the results, reduction factors for the weld can be determined by comparing the specific Wöhler lines, and local material characteristics can be provided for numerical representation of the weld.
Based on the preliminary welding investigations, CastoMag 45640 Ti was identified as the filler metal for the EN-GJS-400-18-LT cast material. The geometry of the weld groove for the main test series was defined in accordance with the welding standard DIN EN ISO 15614-3:2008-6 for testing welded joints with a flank angle of 110 ° and subsequently the cast plates were manufactured with dimensions of 1000 x 600 x 150 mm, Fig. 1.
Circular specimens were subsequently taken from these welded plates transversely and longitudinally to the weld seam. To investigate the integral material properties, the specimens were made significantly longer and taken across the weld seam in order to cover all three areas - base material, heat-affected zone and weld metal. To analyze possible flaws introduced by welding, these specimens were X-rayed before the fatigue tests were carried out, Fig. 2
Among other things, these specimens were used to perform force-controlled tests under axial load with alternating load (R = -1) and threshold load (R = 0) in order to derive the Wöhler lines. An electrical resonance testing machine with a nominal load of 100 kN was used for this purpose. During the tests, the frequency was set in the range between 110 Hz and 120 Hz. During the tests on the integral specimens, it was observed that the failure in the higher-cycle range was primarily triggered by weld-related flaws in the weld, Fig. 3.
As an excerpt from the overall results, Fig. 4 shows the result of the comparison of the Wöhler lines determined on the base material and the integral specimen for alternating load. The base material was characterized with so-called small specimens of 6 mm diameter, which were drawn in over a length of 11 mm. The integral specimens had a larger diameter of 9 mm, since the failure-critical drawn-in area was significantly larger at 50 mm and buckling of the specimens in the elastic-plastic range was thus to be avoided.
The comparison of the Wöhler lines shows that welding has a reducing effect on the fatigue strength and thus on the load-bearing capacity, especially in the higher-cycle range. In addition to an increased scatter of the test results, there is a reduction of the tolerable nominal stress amplitude by about 38 % in relation to a service life of 5∙106 oscillations.
Research project "nodularWELD" - Identification and optimization of welding parameters for repair welding of cast iron components with nodular graphite with adjustment of a defined microstructure to ensure comparable static and cyclic strength characteristics of the weld zone, heat-affected zone and base material; funding code 0324273A, BMWK, PtJ