Experimental fatigue strength validation from the Fraunhofer LBF improves product quality.
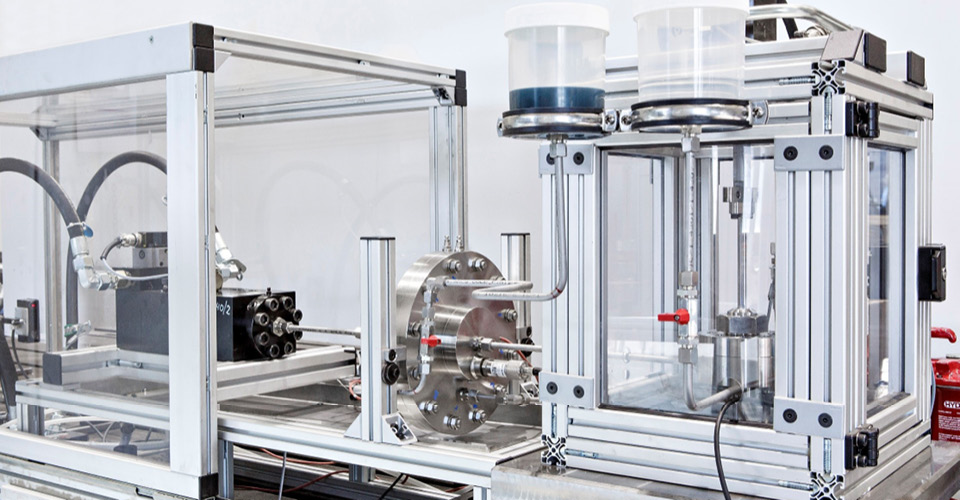
Pressure converters (Fig. 2, item 4) can be used excellently for generating hydraulic loads on components. These typically use hydraulic oil as the medium for actuation and pressure buildup. Elastomer specimens, on the other hand, should only come into contact with the media actually used in operation or compatible with it. Direct contact of elastomer specimens with hydraulic oils should be ruled out unless they are explicitly designed for these media. Special attention must therefore be paid to the excellent lubricating properties of hydraulic oils on the pressure generation side to prevent wear of the piston-cylinder pairing and to the media compatibility of the elastomer specimens.
Therefore, in addition to the mechanical loading of elastomer components of pumps, a concept (Fig. 1) for mechanical-hydraulic loading by means of media separation was developed and implemented at the Fraunhofer LBF as a development project together with Robert Bosch GmbH. The central element is a media separation by means of a flat diaphragm. The diaphragm is surrounded by a specific adaptation (Fig. 3), equipped with an extensive sensor system. The two separate media, hydraulic oil for pressure generation and the test medium, meet at the diaphragm. The adaptation and diaphragm are designed in such a way that the diaphragm realizes a number of load cycles relevant to operational stability, transmits complex pressure curves and avoids overloads, for example in the event of specimen failure. The additional superimposed mechanical load on the specimens is applied by a conventional hydraulic cylinder. Both load paths are combined in the control electronics. The drive signals of the two load paths are determined using the likewise conventional methods of signal iteration. In addition to various force, displacement, temperature and pressure sensors, the system also has a sensor for detecting the mixing of the two separate media, e.g. in the event of damage to the membrane for media separation.
With the test setup presented, elastomer components of pumps could be loaded with realistic operating load signals to safeguard their fatigue life. The setup enables the transfer of comparable load mechanisms from the field to the laboratory and thus the improvement of product quality.