Lebensdauer-Untersuchungen an Elastomer-Komponenten
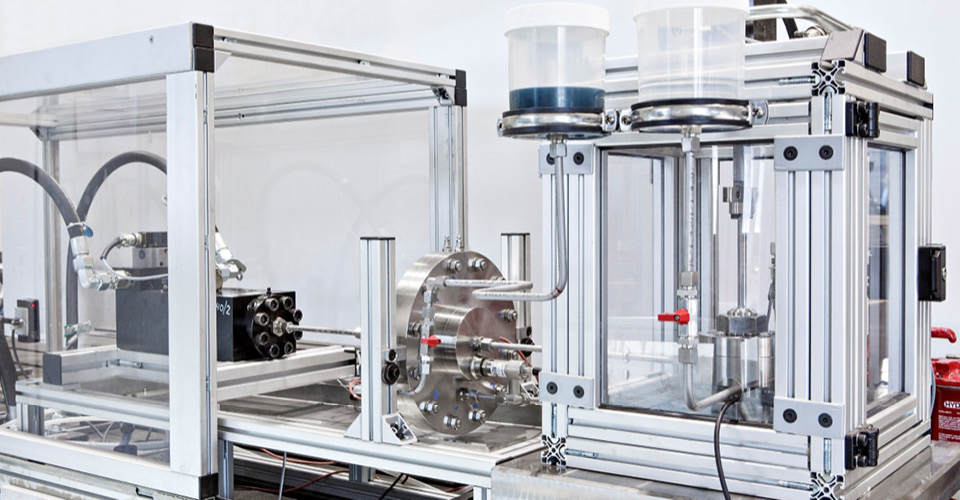
Druckumsetzer (Abb.2 , Pos. 4) können hervorragend zur Generierung hydraulischer Belastungen auf Komponenten eingesetzt werden. Diese verwenden als Medium typischerweise Hydrauliköl zur Ansteuerung und zum Druckaufbau. Proben aus Elastomeren sollten demgegenüber im Versuch lediglich mit den tatsächlich im Betrieb verwendeten oder hierzu kompatiblen Medien in Kontakt treten. Der direkte Kontakt von Elastomerproben mit Hydraulikölen ist auszuschließen, sofern diese nicht explizit für diese Medien konzipiert sind. Den hervorragenden Schmiereigenschaften von Hydraulikölen auf Seite der Druckerzeugung zur Verschleißvermeidung der Kolben-Zylinder-Paarung sowie die Medienverträglichkeit der Elastomerproben muss demnach besondere Beachtung geschenkt werden.
Am Fraunhofer LBF wurde deshalb, ergänzend zur mechanischen Belastung von Elastomerkomponenten von Pumpen, ein Konzept (Abb. 1) zur mechanisch-hydraulischen Belastung mittels Medientrennung als Entwicklungsprojekt gemeinsam mit der Robert Bosch GmbH erarbeitet und realisiert. Zentrales Element ist eine Medientrennung mittels Flachmembran. Die Membran ist von einer spezifischen Adaption (Abb. 3) umgeben, ausgestattet mit einer umfangreichen Sensorik. An der Membran treffen die beiden getrennten Medien, Hydrauliköl zur Druckerzeugung sowie das Prüfmedium, aufeinander. Adaption und Membran sind so konzipiert, dass die Membran eine betriebsfestigkeitsrelevante Anzahl Lastwechsel realisiert, komplexe Druckverläufe überträgt und Überlastungen, zum Beispiel beim Ausfall der Probe, vermeidet. Die zusätzlich überlagerte mechanische Belastung der Proben erfolgt durch einen konventionellen Hydraulikzylinder. Beide Belastungspfade werden in der Regelelektronik zusammengeführt. Die Drive-Signale der beiden Belastungspfade werden mit den ebenfalls konventionellen Verfahren der Signaliteration bestimmt. Neben verschiedenen Kraft-, Weg-, Temperatur- und Drucksensoren verfügt das System auch über einen Sensor zur Detektion der Vermischung der beiden getrennten Medien, z. B. im Falle eines Schadens an der Membran zur Medientrennung.
Mit dem dargestellten Versuchsaufbau konnten Elastomerbauteile von Pumpen mit realitätsbezogenen Betriebslastsignalen zur Absicherung der Lebensdauer belastet werden. Der Aufbau ermöglicht die Übertragung vergleichbarer Belastungsmechanismen aus dem Feld in das Labor und damit die Verbesserung der Produktqualität.