Thermally conductive polyamide 6 blends with high flowability.
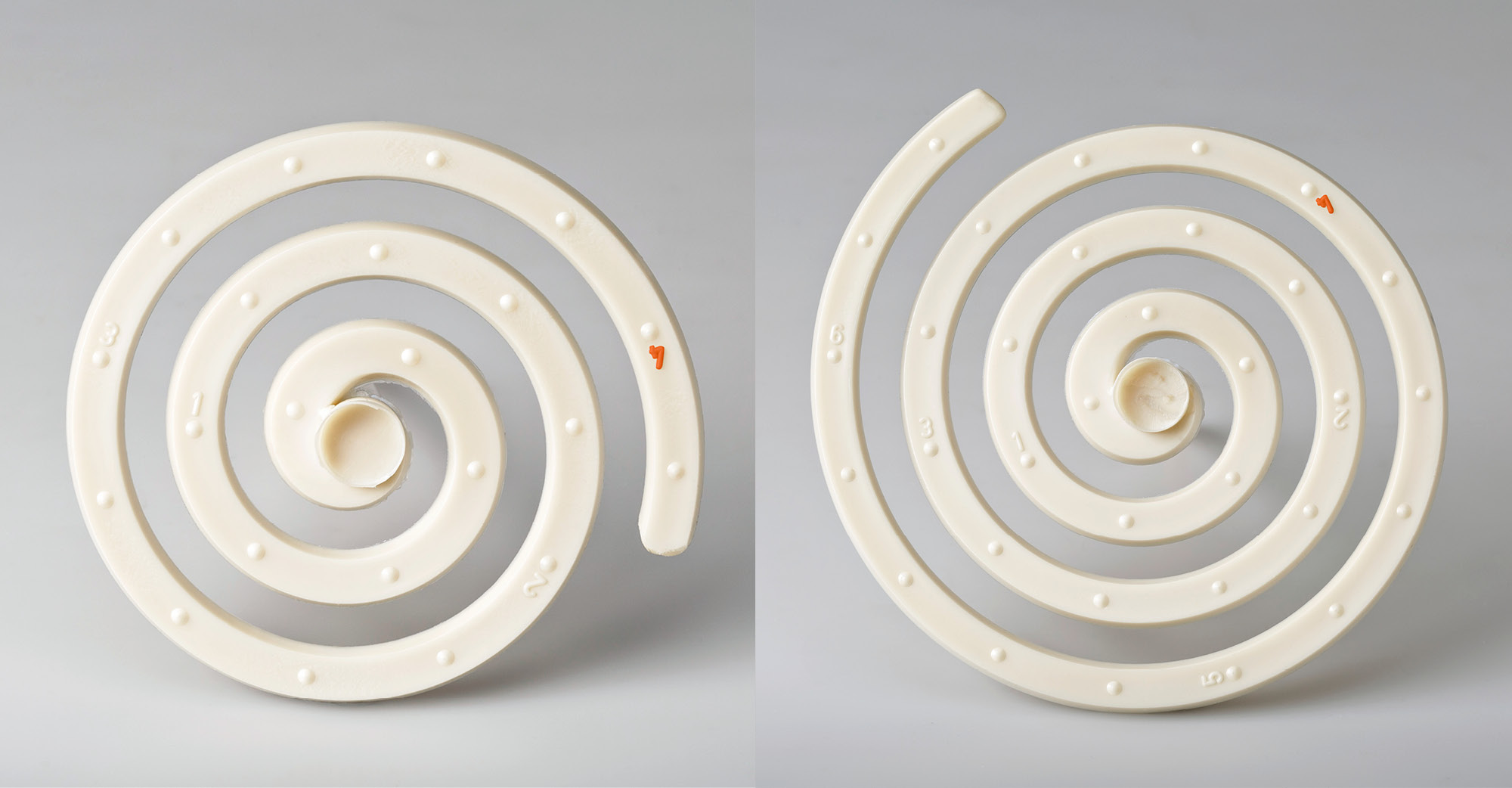
Project HEATCOP
The scientific literature describes polymer blends that are characterized by selective localization of the filler in one of the two polymer phases. Increased levels of thermal conductivity have, for example, been identified in relation to such systems. However, in most cases, these investigations relate to discontinuous (batch) mixers. These findings are not transferable to continuous twin-screw extruders, which are the standard type of equipment used within the plastics processing industry nowadays. In addition, it is not known, or is only rudimentarily known, how those properties of relevance to the majority of applications — such as mechanical properties, fluidity, and so on — are affected. The core aim of the “HEATCOP” project was to investigate these relationships and to determine specific types of interplay between the blend composition, form of process control and resulting material properties. A polymer blend of PA6 (polyamide 6) and HDPE (high-density polyethylene) containing zinc oxide (ZnO) as a thermally conductive filler was selected to serve as the model system for these investigations.
In light of these objectives, various compounding methods (master batch vs. direct compounding), process parameters (such as processing temperatures) and a range of material parameters (e.g., viscosity) were systematically investigated, along with the relationships between the polymer phases, plus filler variables and surface modifications, etc. The findings then enabled a filled polymer blend to be strategically optimized from the perspective of its thermal conductivity, and mechanical and rheological properties. Finally, the Fraunhofer researchers selected a HEATCOP blend system and compared it with a commercially available PA compound with similar filler content.
Despite its high filler content, the HEATCOP blend system that was developed exhibits better impact strength than the commercially available PA compound — with a value of 58 kJ/m2 compared to 30 kJ/m2. At 45 cm, the flow length recorded in the spiral flow test was also considerably higher than for the commercially available compound, thereby indicating that the processing properties are good. However, as expected, the proportion of HDPE in the blend reduces the dimensional stability under heat, with a heat distortion temperature of 82 °C compared to 175 °C for the commercially available PA compound. Consequently, the application potential is to be found in cases where a high level of fluidity or impact strength is needed but the requirements concerning the dimensional stability under heat are lower.
The morphology of blend systems — which results from the interplay between the compound composition and the selected process conditions — is crucial in determining the properties. In this project, various methods were used to investigate the morphology and the distribution of the filler. Within this context, confocal RAMAN microscopy emerged as a suitable method for simultaneously distinguishing between polymer phases and fillers. To enable the analysis of ternary blends with the RAMAN microscope, binary blends consisting of the filler zinc oxide and the relevant polymer — HDPE or PA6 — were investigated first. The researchers were then able to use the data obtained from this to analyze the ternary systems, as shown in Fig. 1.
Using the RAMAN mapping methods developed in this project, no selective localization was identified within the investigated blends. However, during repeat measurements, a certain degree of fluctuation was observable at several cross-sectional points, which can be attributed to local differences in filler and polymer phase distribution.
The “HEATCOP” project has led to the development of an innovative set of thermally conductive polymer blends, which — in addition to their high level of thermal conductivity — are also characterized by improved flow properties and higher impact strength. When the findings are taken together — i.e., those relating to material composition and process control in complex blend systems on the one hand, and those relating to microscopic characterization methods on the other — they enable the efficient development of customer-specific formulations and materials in the context of complex filled polymer blends. The wide variety of possible polymers and combinations means there is plenty of scope for developing functional polymer compounds, but this is not the only factor. The choice of filler is also responsible for determining the set of properties and provides material developers with opportunities for exploring alternative or additional functions of such compounds.
»A huge thank you to Fraunhofer LBF. During the HEATCOP project, cooperation was smooth, unbureaucratic and highly informative. The project meetings were always well structured and communication during the project went without a hitch. It was a win-win situation for everyone involved. If it were possible, this is the point at which I would click the “Like” button!«
Péter Sebö from HPF Minerals
IGF project 19502N titled “New strategies for reducing the filler content in thermally conductive plastic compounds” by the Forschungsgesellschaft Kunststoffe e.V. (FGK) research association was funded via the Arbeitsgemeinschaft industrieller Forschungsvereinigungen “Otto von Guericke” e.V. (German Federation of Industrial Research Associations) as part of the funding program of the collective industrial research (IGF) initiative by the Federal Ministry of Economics and Technology based on a decision by the German Federal Parliament (Bundestag).
This funding is gratefully acknowledged.
Thanks is also due to the plastics research organization Forschungsgesellschaft Kunststoffe e.V.
In addition, we would like to thank the companies represented on the project committee for their professional support.