Virtual test methodology for automated driving functions and vehicles
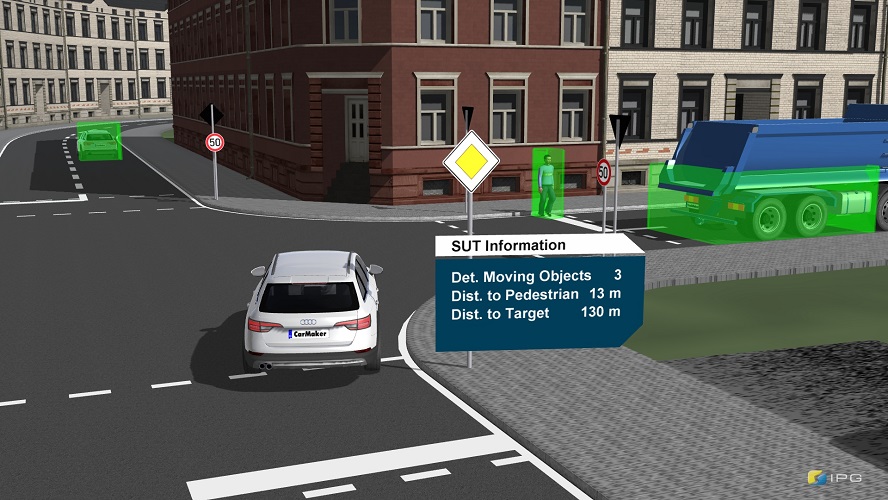
In recent years, fully autonomous (VDA Level 4) and driverless/autonomous (VDA Level 5) driving functions have become a focus of research and development across the globe. They are regarded as a promising approach to solving the challenges of road-based mobility: increasing traffic efficiency, improving traffic safety and reducing emissions. In this context, safety validation plays an essential role. Since in Level 4 and Level 5 systems the driver is no longer continuously available to act as the fallback within the required reaction times, the automation system must be capable of responding to all conceivable traffic situations and potential hazards and manage them safely.
However, with current methods, it is not possible to comprehensively demonstrate that the automation system is capable of doing this, with either simulations or actual driving. The SET Level project aims to develop simulation platforms that can be used to test automated and networked driving functions in urban areas, and to do so flexibly and cost-effectively.
Fraunhofer LBF is developing methods and tools to test the interaction between vehicle systems and automated driving functions using closed-loop simulation in a scenario-based environment. This process involves creating component models of the vehicle, such as powertrains, brakes, steering or vehicle dynamics, as well as of the automated driving functions, such as the vehicle control system (motion control) and interfaces, in order to incorporate these models in different integration environments. This modular structure enables automated driving functions to be tested efficiently with different powertrains, steering or braking systems, both with a variety of vehicle types and in a range of driving situations. Through the interfaces, system models from Matlab/Simulink can be integrated into the virtual test environments, reading and generating standard Open Simulation Interface (OSI) messages. When developing steering, brakes or powertrains, for example, this enables system developers to work entirely in their familiar environment and test their systems using virtual test cases for automated vehicles. At the same time, as part of the test-driven development process, developers of automated driving functions can directly test the interactions of the driving function with the system properties of various target vehicles. Within the closed-loop simulation, different levels of detail can be applied to the submodels to meet the various requirements of each system test in terms of accuracy and simulation speed. To test route planning or parking maneuvers, a vehicle can be represented using simple kinematics, whereas testing sudden avoidance maneuvers or faults, such as the loss of brake fluid or failures in the power electronics, requires a more complex model of the vehicle dynamics and actuators which can reproduce the driving behavior in these situations. In order to support the development of safe, automated vehicles industry-wide and to standardize processes for verifying the safety of vehicles in a reproducible manner, the goal is to make the methods and models available to the public as an open-source tool following completion of the project.
The major German research project SET Level is part of the PEGASUS project family. SET Level further develops the simulation approaches developed in PEGASUS on a broad scale and expands the application to the entire transport area. It is being funded by the Federal Ministry for Economic Affairs and Energy (BMWi) through the “New Vehicle and System Technologies” program. A total of 20 project partners from industry and science are working together on this project.
Project partners involved in SET Level: ADC Automotive Distance Control Systems GmbH (a Continental AG company), Audi AG, BMW AG, dSPACE GmbH, German Aerospace Center Institute of Transportation Systems, German Aerospace Center Institute of Systems Engineering for Future Mobility, ETAS GmbH, Ford Germany, Fraunhofer LBF, Research Center for Information Technology (FZI), IPG Automotive GmbH, MAN Truck & Bus AG, Opel Automobile GmbH, PROSTEP AG, Robert Bosch GmbH, RWTH Aachen (Institute for Automotive Engineering), Technical University of Braunschweig (Institute of Control Engineering), Technical University of Darmstadt (Automotive Engineering), Volkswagen AG, ZF Friedrichshafen AG.