Schnelle Untersuchungen zur Verarbeitungsstabilisierung am Beispiel von Polypropylen
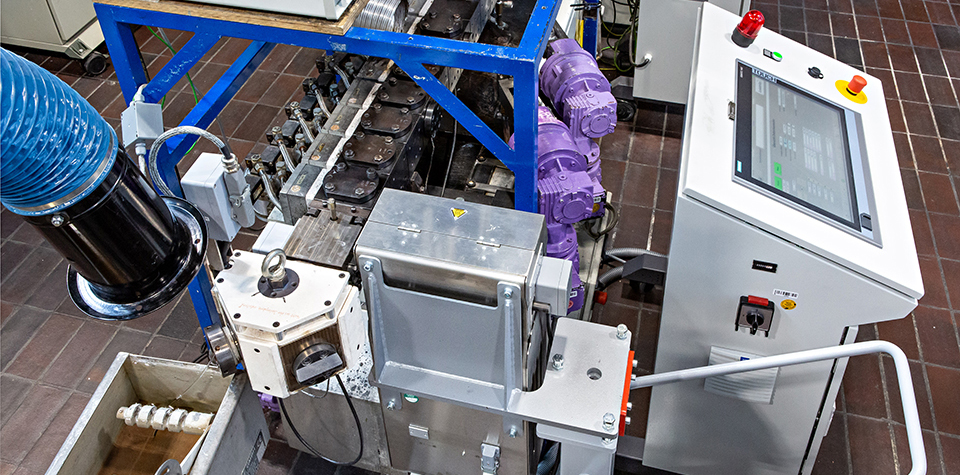
Alle organischen Substanzen und somit auch Kunststoffe wie Polypropylen (PP) unterliegen in Gegenwart von Sauerstoff einem Autooxidationsprozess. Dieser findet bei den hohen Temperaturen der Schmelzeverarbeitung wie der Compoundierung und dem Spritzguss erheblich beschleunigt statt. Die Folge bei PP ist ein Abbau der Polymerketten, also eine Degradation der Molmasse. Antioxidantien verlangsamen den Abbau. Ohne diese Additive ließen sich die bekannten Gebrauchsgegenstände gar nicht erst herstellen. Bisher wird bei der Entwicklung von neuen Compounds der optimale Anteil an Antioxidantien in umfangreichen und damit kostenintensiven Versuchsreihen ermittelt. Schließlich möchte der Verarbeiter die Eigenschaften des Kunststoffs bestmöglich erhalten. Bei der Rezyklatgewinnung aus Altmaterialchargen stark wechselnder Qualität sind langwierige Vorversuche hingegen kaum möglich. Forschende am Fraunhofer-Institut für Betriebsfestigkeit und Systemzuverlässigkeit LBF sehen in online-rheologischen Untersuchungen eine vielversprechende Methode, den Entwicklungsprozess zu beschleunigen.
Wie alle organischen Verbindungen werden auch Kunststoffe durch Luftsauerstoff geschädigt, d.h. oxidiert. Eine radikalische Kettenreaktion, initiiert durch Licht oder Wärme, führt zur Bildung von OH-Radikalen und sogenannten Hydroperoxiden, die die Polymerketten sehr rasch abbauen. Bestmögliche Stabilisierung wird heute durch die synergistische Wirkung von zwei Antioxidantientypen erreicht. Das primäre Antioxidans zur Deaktivierung des OH-Radikals enthält häufig phenolische Strukturen. Sekundäre Antioxidantien, z.B. organische Phosphite fangen die Hydroperoxide ab. Die notwendige Stabilisatorkonzentration und das Verhältnis der beiden Antioxidantien sind abhängig vom jeweiligen Kunststoff, den Verarbeitungsbedingungen und von der Anwendung. Im Maßschneidern des Antioxidantienverhältnisses und der Gesamtmenge liegt eine enorme Chance beste Produktqualität bei minimalen Kosten zu erzielen.
Da bei den hohen Temperaturen der Schmelzeverarbeitung der Oxidationszyklus millionenfach schneller abläuft als bei der Umgebungstemperatur, kommt den Antioxidantien als Verarbeitungsstabilisatoren eine besondere Rolle zu. Für jedes Compound gibt es eine optimierte Stabilisatorkonzentration, oberhalb derer keine Verbesserung mehr erreicht wird. Diese Menge muss bei der Entwicklung von Kunststoffcompounds vor dem Hintergrund von Ressourcenschonung und Wirtschaftlichkeit gezielt ermittelt werden. Hierzu werden bisher Compounds mit unterschiedlichen Anteilen der Antioxidantien in Form von Konzentrationsreihen hergestellt. Die Charakterisierung geschieht offline mittels verschiedener Tests, wie z. B. Messung der Volumenfließrate (MVR, DIN 1133-1). Belastbare Ergebnisse erhält man somit erst nach dem Compoundierschritt.
Handelsübliche Neuware-Typen sind häufig vom Hersteller oder Compoundeur mit den notwendigen Stabilisatorpaketen gebrauchsfertig ausgerüstet. Bei den Altkunststoffen in Wertstoffströmen, die zur Herstellung von Rezyklaten eingesetzt werden, sind die Stabilisatoren in unterschiedlichem Maß verbraucht. Somit kommt es bei der Compoundierung des Mahlguts zu Rezyklaten und deren Weiterverarbeitung, z. B. im Spritzgussprozess, darauf an, die Stabilisatoren in Anteilen genau passend zu den Kunststofftypen und deren Alterungszustand zu ergänzen.
Das bei der Entwicklung von Neuware-Compounds praktizierte Vorgehen erscheint hierfür als zu aufwändig. Ein Ansatz, bei der Rezyklatherstellung einfach „genug“ Stabilisator hinzuzugeben, ist vor dem Hintergrund einer konsequenten Kreislaufwirtschaft ungeeignet oder zu kostspielig. Weiterhin gibt es für die Verträglichkeit von Stabilisatoren mit dem Polymeren eine Obergrenze. Denn der Kunststoff wird nicht nur ein second, sondern auch ein third, fourth usw. Leben erfahren. Während eines jeden Lebenszyklus‘ verbrauchen sich bestimmungsgemäß die Stabilisatoren, wobei deren Folgeprodukte im Kunststoff verbleiben. Umso wichtiger ist es, bei der Rezyklatgewinnung nur die unbedingt erforderliche Menge an Stabilisator hinzu zudosieren.
Wir am Fraunhofer LBF verfolgen den Ansatz, bereits während der Compoundierung online die Schmelze zu charakterisieren, um sofort Aussagen über die Wirksamkeit der aktuellen Stabilisatorzugabe zu gewinnen.
Mit einem Online-Rheometer, das hinter den Schneckenspitzen an einen Doppelschneckenextruder angeflanscht ist (Abb. 1), messen wir die Fließkurven sowohl der Scher- als auch der Dehnviskosität.
In ersten Untersuchungen an einem wenig stabilisierten Neuware PP wurde für ausgewählte Drehzahlen die Menge an zudosiertem Stabilisator variiert. Mit zunehmendem Stabilisatorgehalt verschieben sich die Fließkurven zu höheren Viskositätswerten, was auf einen verringerten prozessbedingten Abbau schließen lässt (Abb.2a). Offline-Untersuchungen an den entsprechenden Proben ergeben im gleichen Sinne höhere Molmassen, wodurch die Annahme des verringerten prozessbedingten Abbaus klar bestätigt wird. Im log-log-Plot zeigt sich zwischen der Nullviskosität (aus dem Fit eines einfachen Viskositätsmodells an die Fließkurven) und der massengemittelten Molmasse Mw entsprechend der Theorie ein linearer Zusammenhang (Abb. 2b).
Ab einem bestimmten Additivanteil kommt es zu keiner weiteren Viskositätszunahme. Damit ist für die vorliegenden Prozessbedingungen die Grenzkonzentration des Stabilisators erreicht, oberhalb derer sich keine weitere Verbesserung erzielen lässt. Diese Situation wurde bei den geschilderten Versuchen bei der Verarbeitung mit 100 rpm und einem Stabilisatoranteil von 0.2% erreicht (Abb. 2c).
Diese Versuche wurden nun auf je ein post-industrial und post-consumer Recycling PP übertragen. Das post-industrial PP aus Anfahrmaterial und Angüssen von Spritzgussprozessen weist noch einen hohen Stabilisatoranteil auf. Somit lassen sich hier mit Stabilisatorzugaben über 0.1% hinaus keine signifikanten Verbesserungen beim Erhalt der Molmasse erzielen - die Fließkurven für die untersuchten Stabilisatorzugaben liegen dementsprechend nahezu übereinander (Abb. 3a). Bei dem post-consumer PP sind die Antioxidantien in hohem Maße verbraucht, womit eine signifikante Schädigung bei der Verarbeitung verbunden ist, die sich in einer niedrigen Viskosität/Fließkurve bemerkbar macht (Abb. 3b). Für eine optimierte Stabilisierung und minimierte Schädigung des Rezyklats ist hier eine Zugabe von 0.5% Additiv erforderlich.
Die online-rheologischen Messungen erlauben es also, aussagekräftige Rückschlüsse auf die für die jeweilige Altkunststoff-Charge sinnvoll hinzuzufügende Menge an Antioxidantien zu ziehen.
Die hier vorgestellte Online-Rheologie steht im Technikum des Fraunhofer LBF Projektpartnern zur Verfügung. Sie ermöglicht es Verarbeitern, unmittelbar Informationen zur Auswirkung eines Prozess-Stabilisators zu erhalten und damit kostengünstig die Rezeptur zu optimieren.
Zusätzlich spiegeln die Fließkurven der Dehnviskosität die Stabilität der Schmelze wider. Im Gegensatz zur Scherviskosität wird die Dehnviskosität auch sehr empfindlich durch den Faseranteil und die Faserverteilung beeinflusst. Da die Schmelzestabilität ein wichtiges Kriterium für die Verwendung eines gegebenen Compounds für Blasformverfahren ist, kann die Online-Rheologie den Compoundentwickler auch hierbei unterstützen.