Hybride Batteriearchitektur für Schiffe
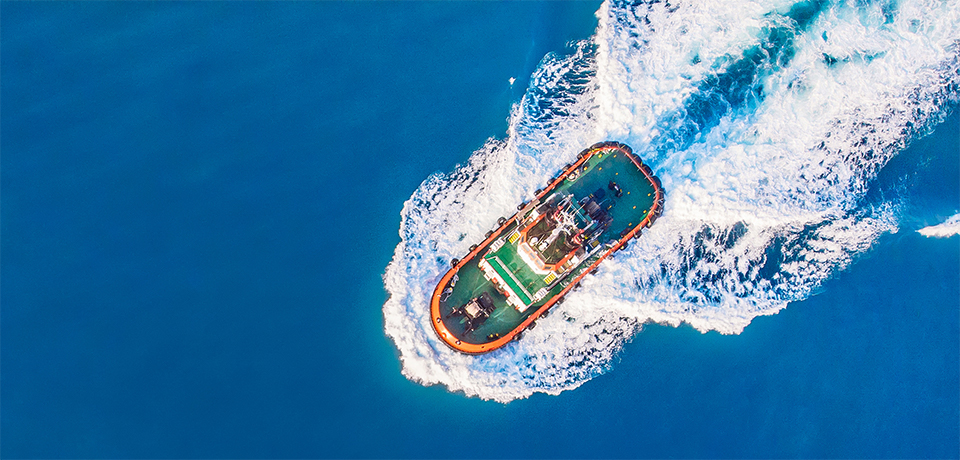
Batterielösungen für Schiffe sind in der Regel maßgeschneidert und wenn überhaupt für Kleinstserien, was zu hohen Kosten führt. Hinzu kommt, dass ein einziger Batterietyp sowohl für das Abdecken des hohen Energiebedarfs, z. B. zur Aufrechterhaltung der Reisegeschwindigkeit, als auch für hohe Leistungsspitzen, z. B. beladen im Hafen, verwendet wird. Eine einzige Zelltechnologie kann jedoch nicht beide Anforderungen abdecken. Daher werden Batterien um den Faktor 2 bis 10 überdimensioniert, was ebenfalls hohe Kosten verursacht.
Im EU-Verbundvorhaben SEABAT wurde ein Hybridkonzept entwickelt, das auf der Kombination von Hochenergie- und Hochleistungsbatterien mit einem neuartigen Wandlerkonzept basiert.
Das hybride Batteriesystem besteht drei Architekturebenen: Modul-, Strang- und System-Ebene. Die System-Ebene umfasst das gesamte Batteriesystem und regelt die verschiedenen Stränge. Jeder Strang verwaltet einzelne Module, um die entsprechende Gleichspannung bereitzustellen, während jedes Modul, ob Hochenergie- oder Hochleistungsmodul, die jeweiligen Lithium-Ionen Batteriezellen regelt.
Das Herzstück sind die Batteriemodule, von denen es zwei Typen gibt: Hochenergie (HE) und Hochleistung (HP). Der Hauptunterschied besteht in der verwendeten Zelltechnologie, nämlich NMC bzw. LTO. Jedes Modul besteht BMS seitig aus einem Master- und Slavesystem und einem Gleichspannungswandler.
Das Design der SEABAT-Module basiert auf dem, aus dem Automobilsektor bekannten, Plattformdesign, das identische Komponenten und Baugruppen für beide Modultypen (HP und HE) nutzt. Der Ansatz, so viele Gleichteile wie möglich zu nutzen, führt zu geringeren Kosten, sowohl Hardware- als auch montageseitig.
Die beiden Modultypen unterscheiden sich letztlich nur in der Art der Lithium-Ionen-Zellen (HP oder HE) und damit verbunden der Führung der elektrischen Anschlussschienen (Bus bars) und anhand der Leiterplatinen zur Zellüberwachung. Alle anderen Komponenten wie Gehäuse, Kühlsystem, Gleichspannungswandler, Zellfixierung, Elektronikboards, Halter zur Fixierung weitere Komponenten und bis hin zu den Schrauben sind identisch. Die beiden Zelltypen mit ihren unterschiedlichen Abmessungen werden durch eine mittige Ausrichtung und einer zentralen und identischen Befestigungseinheit fixiert. Zusätzlich sind sie seitlich durch unterschiedliche Positionen der seitlichen Zellbefestigung im Modul fixiert. Die Komponente selbst zur seitlichen Zellfixierung ist für beide Modultypen gleich.
Das Modul-Gehäuse selbst besteht aus drei Komponenten mit unterschiedlichen Materialien: Bodenplatte aus Aluminium, Abdeckung aus Stahlblech und Duroplast und einer Schnittstellenplatte aus Aluminium für die elektrischen Anschlüsse. Für die Modulabdeckung wurde in Leichtbauweise ein zweilagiges Design gewählt. Die innere Lage besteht aus einem sogenannten Ablationsmaterial, was in diesem Anwendungsfall ein Duroplast mit mineralischen Füllstoffen ist, der durch Aramid verstärkt wird. Bei der äußeren Lage handelt es sich um Chrom-Nickel-Blech. Das Ablationsmaterial wird unter dem Einfluss heißer abrasiver Medien, wie dem partikelhaltigem Gasstrahl, der bei einem thermischen Durchgehen eine Lithium-Ionen Zelle aus dieser ausgestoßen wird, geopfert. Dies sichert die mechanische Integrität der Blechhaube bei einem solchen Ereignis.
Basierend auf Ergebnissen von bei CEA durchgeführten Tests auf Zellebene, wie Überladungs- und Übertemperaturtests, wurde das Gehäuse inklusive Sicherheitsentlüftungsventilen zum Ausblasen der bei einem thermischen Durchgehen entstehenden Gase ausgelegt. Zur Validierung des Gehäusedesigns wurde beim Projektpartner CAE auf Modulebene ein thermal runaway bei beiden Modultypen ausgelöst. Die Ergebnisse entsprachen allen Erwartungen und beide Modultypen haben somit den Test erfolgreich bestanden.
Dieses Projekt wurde durch das Forschungs- und Innovationsprogramm Horizont 2020 der Europäischen Union unter der Finanzhilfevereinbarung Nr. 963560 gefördert. Das Seabat-Projektkonsortium besteht aus 15 Partnern aus 8 verschiedenen EU- und assoziierten Ländern.